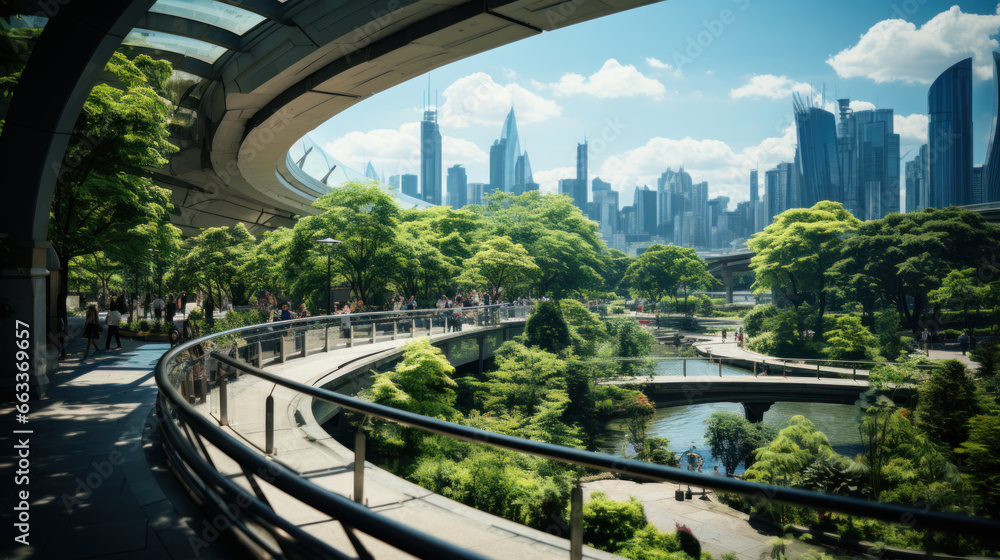
Urban areas face rising temperatures from the combined effects of climate change and the “urban heat island” phenomenon. Concrete and asphalt trap heat, creating hotter cities, escalating energy demands, and endangering vulnerable populations. To mitigate these effects, solutions must address the problem across all scales: city, neighborhood, street, building, and individual levels.
City-Level Strategies
At the city scale, urban planning focuses on creating cooler environments by improving airflow, increasing plant cover, and reducing heat-retaining surfaces:
- Urban Planning and Cool Corridors: Designing open spaces and cool corridors encourages air circulation and reduces heat concentration.
- Increasing Plant Cover: Initiatives like Paris’ Oasis Project transform schoolyards into green spaces, doubling as cool islands and heat refuges.
- Low-Emission Zones (ZFE): Reducing vehicular traffic in cities cuts emissions, indirectly lowering heat retention.
- Urban Water Management: Large-scale rainwater management systems and urban basins help infiltrate water into the soil. This not only prevents flooding but also encourages evaporation, naturally cooling the air during heatwaves.
Neighborhood-Level Strategies
Neighborhood interventions tackle heat through surface treatments, targeted greenery, and smart solutions:
- High-Albedo Materials: Reflective materials reduce heat absorption, like those used in Paris’ “cool islands.” High-albedo materials are surfaces that reflect more sunlight than they absorb, helping to lower surface temperatures.
- Vegetation and Cool Islands: Projects like Urban Canopée integrate vegetation into neighborhoods, while ENGIE Lab Crigen’s Skycooling panels provide shade-based cooling.
- Water Permeation: Soil desilting and localized rainwater infiltration enhance evaporation, which cools the surrounding air naturally. Incorporating small water features like ponds or fountains within neighborhoods can amplify these cooling effects.
Street-Level Strategies
Streets act as heat hotspots, but targeted solutions can reduce their thermal footprint:
- Draining Pavements: Products like Holcim’s concrete, a permeable concrete Hydromedia, allow rainwater to infiltrate the soil, supporting evaporation and natural cooling.
- Green Walls and Photovoltaic Shades: Vegetated walls and shaded walkways lower street temperatures while improving aesthetics and functionality.
- Localized Water Features: Incorporating fountains, small basins, or artificial streams along streets can provide significant localized cooling effects.
Building-Level Strategies
Buildings are central to urban cooling, as they represent a significant proportion of heat storage:
- Green Roofs: Vegetative layers provide natural insulation and cooling, reducing the heat stored by buildings.
- Reflective Paint: Products like Cool Roof reduce heat absorption, keeping interiors cooler.
- Advanced Insulation: Aerogels, a cutting-edge material known for their lightweight properties and high thermal resistance, can significantly reduce heating and cooling costs by providing superior insulation compared to traditional materials.
- Bio-Reactive Facades: Innovations like XTU Architects’ microalgae facades actively regulate temperature by producing oxygen and absorbing heat.
- Rainwater Harvesting: Buildings can integrate systems to collect rainwater, which can then be used for evaporative cooling or irrigation for rooftop and vertical gardens, further reducing heat buildup.
Individual Actions
Individual behaviors also play a vital role in reducing urban heat:
- Soft Mobility: Walking, cycling, and using public transport help reduce vehicular emissions and heat contributions.
- Urban Greening: Individuals can plant greenery at home, install small water features in gardens, or volunteer for local tree-planting initiatives to enhance cooling.
- Water Stewardship: Households can promote cooling by managing rainwater infiltration with permeable garden designs, rain barrels, or bioswales to ensure water is available for natural evaporation processes.
Cooling urban environments requires a multifaceted approach across different scales. From city-wide planning and water management to individual actions like soft mobility, these strategies not only provide immediate relief from heat but also promote the long-term sustainability of urban life. Addressing the urban heat island effect is a pressing necessity as cities prepare for increasingly extreme temperatures in the decades ahead.
.
2 Key Figures
4
Temperatures can be 1 to 4°C higher than surrounding rural areas due to the presence of heat-retaining infrastructures like concrete and asphalt.
15%
A 10% increase in tree cover in cities reduces surface temperatures and lower energy consumption needs for cooling by around 15%.
.
3 startups to draw inspiration from
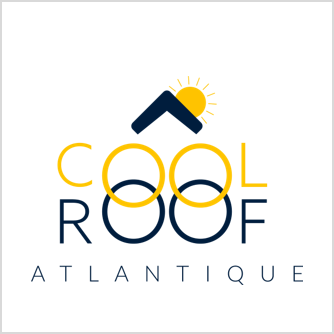
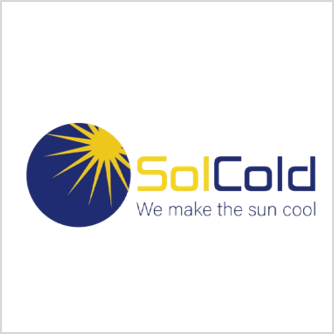
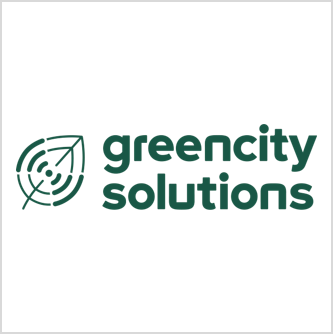
CoolRoof
French-based startup specialized in reflective coatings for rooftops and pavements to reduce heat absorption in cities, lowering temperatures and energy consumption.
SolCold
A materials startup from Israel that creates innovative coatings which cool buildings by converting heat into light, reflecting sunlight to reduce urban temperatures.
Green City Solutions
German startup that develops urban green spaces using “CityTree,” a smart, air-purifying moss wall that cools and cleans the air in densely populated areas through IoT integration.
Interested in a startup landscape or in an insights report?
Please fill out our contact form so that we can get back to you very quickly with our product offer.
Want to subscribe to our 123Fab?
Fill out our form to receive the latest insights into your inbox.

Context
Our client has developed a strong Open Innovation activity in order to fuel its transformation. In this context, our client asked us to conduct a deep dive study on high-temperature superconductors.
Mission
We carried out a study to define the go-to-market strategy:
- Market study on megatrends and key forces shaping the industry
- Competitor benchmark and illustration of large-scale deployments
- Funding analysis and illustrations of the latest investments
- Patent volume and key patent filer analysis
- Sourcing of all startups in the field
- Interviews with these startups to create fact sheet one-pagers
Key figures
50
Key players identified
36
Live installations mapped
5
Interviews conducted
10
Team members engaged
123Fab #89
1 topic, 2 key figures, 3 startups to draw inspiration from
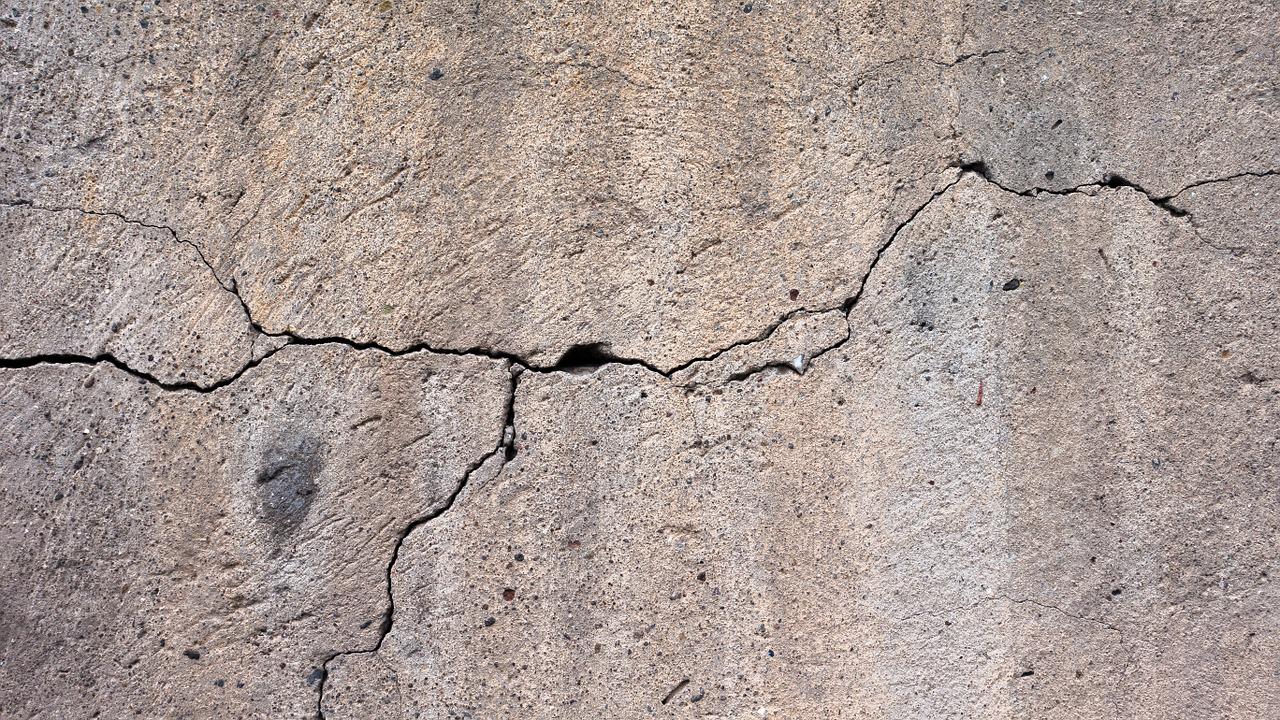
The March 2022 report by The Court of Auditors indicates that the proportion of French road surfaces requiring maintenance work has risen from 43% to 53% over the last ten years. This increase is hardly surprising given the impact of climate change (freeze-thaw, drought, flooding, etc.) and the increasing weight of vehicles, damaging the tarmac as they pass. As a result, the State is obliged to invest more over the next few years and the law on the orientation of mobility has set a financial trajectory up to 2027 and beyond – eventually exceeding 1 billion euros per year. However, one technology could radically change the situation in the future: self-healing materials.
Since the 2000s, a number of self-healing materials have emerged. They use healing agents such as embedded microcapsules filled with glue-like chemicals or even living micro-organisms, the use of materials with internal vascular circulation like blood, shape-memory materials, or reversible polymers. Self-healing materials offer many promising possibilities in the construction sector, but also have potential applications in everything from 3D nanostructure to spacecraft.
Concrete
Concrete is the second most used substance on the planet after water, according to The Guardian, and forms the basis of modern construction. However, it comes at a huge environmental and financial cost, both in terms of the energy used to create it and its condition after use. Start-up Basilisk, a pioneer in this field, is now commercializing its self-healing concrete solution. The technology is based on an additive added to the concrete mix, consisting of particles that contain dormant bacteria and nutrients. Air or water generated by a crack will awaken bacteria which, by feeding on these nutrients, will fill the cracks, creating limestone. Precast group JP Concrete has signed an exclusive agreement to use Basilisk’s Sensicrete compound in its products and market self-healing concrete in the UK. However, the cost of this method is significant. The price per square meter would be double that of conventional concrete. Other initiatives based on other techniques have been developed to reduce the cost of the technology. This is the case with enzymatic construction material (ECM), which has been patented and produced by Enzymatic Inc. as a building material. Composed of carbonic anhydrase, an enzyme found in living cells, it is able to self-heal and remove greenhouse gas from the air for safe storage. It costs about $168 per square meter (compared to standard concrete at around $125 per square meter) but its energy cost is much lower. While it is not yet strong enough for apartment buildings, it could be used for smaller projects requiring less load, such as the side of a house.
Asphalt
Traditionally, asphalt has been used as a binder with concrete for road laying. Exposure to vehicle use, sunlight, rain, and other natural circumstances causes roads to degrade over time. As a result, asphalt roads lose their natural binding capabilities and require frequent repair and maintenance. Start-ups such as Self Healing Materials are developing self-healing asphalts with specific properties as a solution to improve the lifespan of pavements. By introducing steel fibers into the asphalt and using an induction machine to heat the iron molecules, the energy goes directly to the mortar, which melts briefly where the cracks form. This allows the asphalt to return to its original structure. With this technique, the lifespan of the asphalt, initially ten to twelve years, is extended to twenty years. The start-up manufactures other self-healing materials such as plastics, coatings, rubber and concrete, notably through microencapsulation, polymer use and vulcanization techniques.
Steel and aluminium
In a similar vein, solutions are emerging to self-heal structural steel and aluminium surfaces subject to damage and exposure to corrosive environments. Start-up Autonomic Materials has developed a patented, award-winning self-healing technology based on microcapsules that contain healing agents – a mixture of resins, corrosion inhibitors and adhesion promoters. When the coating is damaged, the microcapsules embedded in the coating are broken, releasing the healing agent into the damaged site where it hardens, maintaining the coating’s adhesion and ability to protect the underlying surface. The startup’s product can be used for construction, agricultural equipment, mining equipment, tanks, shopfitting, etc. Since its creation, the startup has raised more than €13 million, notably from Phoenix Venture Partners and Solvay Start-Ups Accelerates Innovation. It completed its series C in 2020.
Although research into self-healing materials dates back a few years, the sector is constantly developing and experiencing new technological advances, which are gradually reducing costs. This type of material is becoming increasingly important in the construction sector and is a key strategic aspect for all groups and start-ups in the sector, as well as for VCs. They are also often associated with emission reduction with the introduction of materials capable of capturing and storing CO2 from the air, which makes it an even more important issue for the future.
2 Key Figures
The self-healing materials market is anticipated to reach $34.4 billion with a CAGR of 95.4% between 2021 and 2026
Market Data Forecast
+100 self-healing materials startups
StartUs Insights
3 startups to draw inspiration from
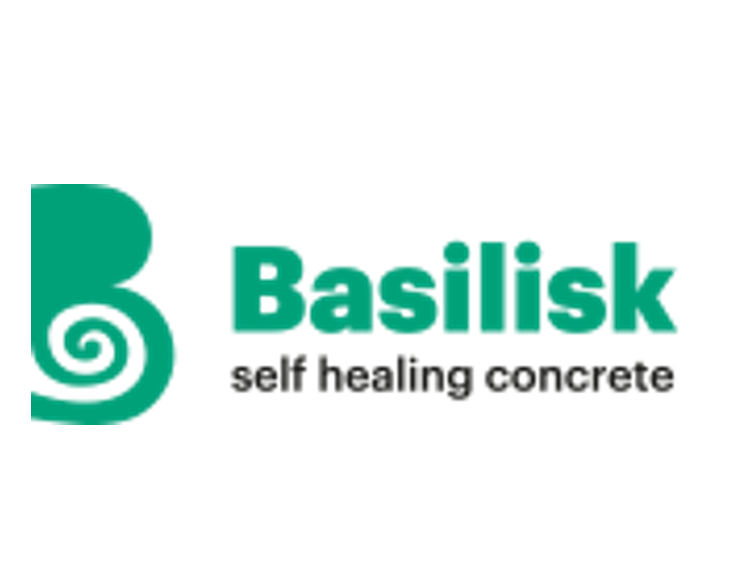
Basilisk
The Dutch startup has developed and patented a self-healing concrete solution in collaboration with the Delft University of Technology. This is based on the principle of self-healing cracks through the use of micro-organisms that produce limestone. The technology is applicable to both existing and new structures. Currently, cracks up to 0.8 mm wide can be treated and repaired within 3 weeks, thus improving the service life of structures.
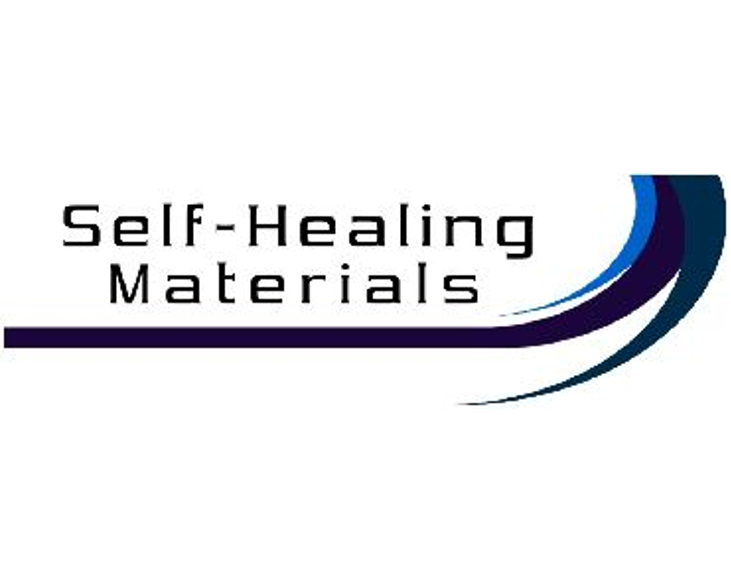
Self-Healing Materials
Slovakian startup Self Healing Materials creates self-healing asphalt, among other materials they work on. The startup helps heal torn roads by way of induction heating as embedded steel fibers conduct the energy and directly transfer it to the mortar. Additionally, the startup manufactures other self-healing materials such as plastics, coatings, rubber, and concrete.
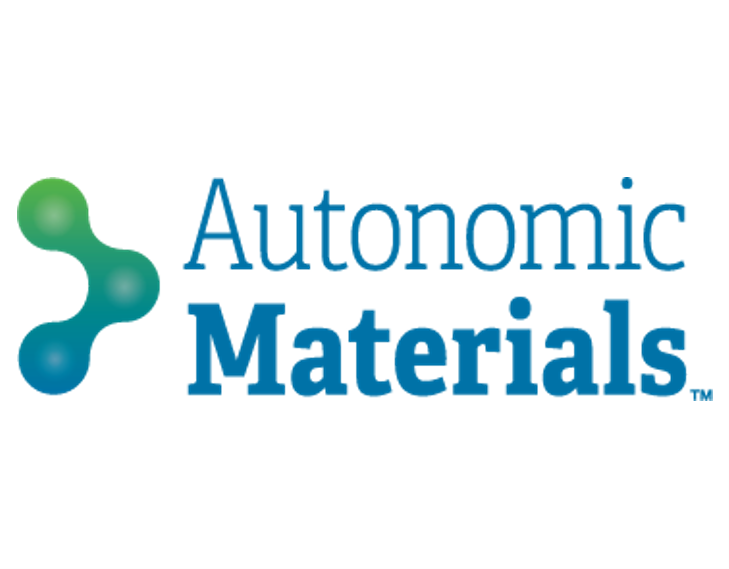
Autonomic Materials
The US startup has developed patented self-healing technology, which, when incorporated into coatings, helps them maintain their protective ability after damage. The technology is based on microcapsules that contain healing agents – a mixture of resins, corrosion inhibitors and adhesion promoters. It contributes to minimising the CO₂ impact of asset maintenance.
Interested in a startup landscape or in an insights report?
Please fill out our contact form so that we can get back to you very quickly with our product offer.
Want to subscribe to our 123Fab?
Fill out our form to receive the latest insights into your inbox.
123Fab #49
1 topic, 2 key figures, 3 startups to draw inspiration from
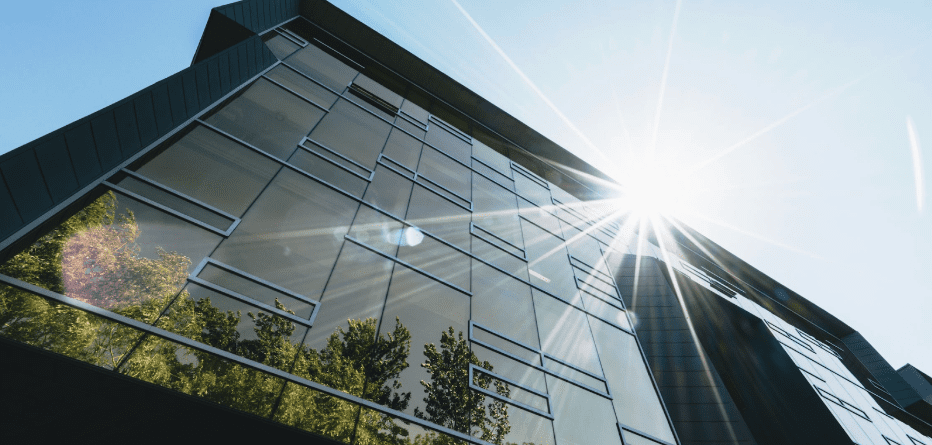
In May 2021, Barbara Pompili, the French Minister of the Ecological Transition, announced the selection of 215 startups and SMEs for the GreenTech Innovation label, among which 45 are solutions for more sustainable buildings and better energy efficiency. These startups will be supported by the government for their development and commercialization. This is one example out of many government initiatives to boost the building energy efficiency and renovation market.
The International Energy Agency estimates that the building sector is responsible for 42% of global electricity consumption. Energy efficiency is about performing the same tasks with less energy. Buildings can go down to net-zero energy consumption which means that the total amount of energy used equals the amount of renewable energy created on-site or by off-site renewable sources. As most of the energy used in buildings is for maintaining a comfortable temperature (heating or cooling) and good ventilation, effective thermal insulation has a major impact on energy consumption. Thus, in the context of global efforts to reduce energy consumption and reach the 2050 net-zero target, buildings’ energy efficiency is more than necessary. To achieve it, most of the efforts need to focus on renovating and retrofitting existing buildings, rather than new performant ones, as they will represent more than 90% of 2050’s properties. It has ecological and economic benefits as it reduces the amount of energy consumed (and associated GHG emissions) while lowering the energy bill for the occupants. The top priority are the « thermal strainers » which are the buildings with the worst energy efficiency, where cold enters in the winter and heat enters in the summer. In France, they correspond to the buildings with an energy consumption above 330 kWh /sqm /year, which are ranked F or G. There are three main thermal losses. The surfaces (roof, walls, windows, ground floor) between the interior and exterior account for up to 80% of energy loss. Then, the controlled mechanical ventilation and ventilation grilles, which ensure the renewal of indoor air, make up to 20% to 25% of energy loss. Finally, the thermal bridges, which are points in construction where the insulation barrier is interrupted, contribute to 5% to 10% of heat loss. Thus, efforts should be put on external cladding and filling the thermal bridges to retrofit the existing buildings.
Different types of innovative solutions exist to improve buildings’ energy efficiency:
- Measure: Many sensors and IoT technologies have been developed to compute more accurately buildings’ energy consumption. French start-up Smart Impulse, for instance, has developed a smart meter to measure the electricity consumption of buildings by usage (lighting, IT, heating, etc.) which gives insights on potential energy savings.
- Retrofit: Picking the right materials highly contributes to buildings’ efficiency. New technologies have been developed to avoid energy loss, such as the thermal reflective resin for roofs of the start-up Cool Roof. Their solution aims to return roughly 90% of the solar heat. It protects the roof from physical damage while maintaining a comfortable temperature inside the building. Moreover, the Dutch EnergieSprong approach is being deployed in France, UK, and Germany for a quick and affordable retrofit of the existing buildings into zero-energy ones.
- Optimize: There are more and more integrated energy management systems that measure and autonomously regulate energy consumption. Thanks to numerous sensors and IoT devices, the American start-up Budderfly provides a solution optimizing entire buildings’ energy consumption.
Although these solutions are very promising, some challenges still have to be overcome. First, renovation takes time obtaining the required permits for structural renovations, finding the right partners, and performing it. Then, even if some startups and companies are offering affordable solutions, it remains costly and often requires important initial investments. All the more so as energy-efficiency goals are often secondary to economic considerations and are not taken into account in the property’s life-cycle costs. Another barrier is the fragmentation of the construction industry, which involves many different actors and stakeholders who have varied interests. Finally, the diversity of the social and regulatory contexts – within the EU for instance – makes it hard to scale solutions.
However, most countries are addressing this issue and implementing associated regulations, incentives, and climate change targets. In France, the government has put in place financial support for buildings renovation but also biding policies like the interdiction from 2028 to rent a flat or house with an energy performance rated F or G. In 2021, the French government announced 6.6 million euros for buildings’ energy renovation over 2 years in their economic recovery plan. Another example of an efficient policy in California where homes and buildings are relatively energy-efficient today. Since 1975, the California Public Utility Commission has directed the investor-owned utilities to commit over $US 5 billion to energy efficiency programs, 85% of which has been targeted at retrofit energy efficiency investments in existing buildings. For instance, Netflix has equipped its headquarters in Los Gatos with View dynamic glass, which controls how much light gets in and contributes to saving up to 20% of energy costs.
To conclude, there are a lot of startups that have spotted an opportunity in improving buildings’ energy efficiency, whether it is with hardware and high-tech materials or smart software. The market is far from being addressed, and governments are multiplying incentives to do so, which is very promising as soon as people are willing to make the investment.
2 Key Figures
637 building energy efficiency & management startups
registered by Tracxn
Global efficient building market expected to reach $253 Bn by 2027
The global efficient building market was estimated at $146 Bn in 2020 and is expected to reach $253 Bn by 2027, at a CAGR of 8.15%.
3 startups to draw inspiration from
This week, we identified three startups that we can draw inspiration from: Sensor Flow, View, and 75 Fahrenheit.
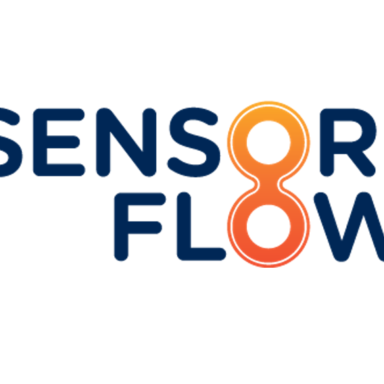
SensorFlox
SensorFlow is a Singapore-based start-up that develops room automation and energy management systems focussed on the hospitality sector. Its solution helps automate a building to optimize energy consumption. It includes occupancy sensors, smart thermostats, door sensors, and split unit thermostats.
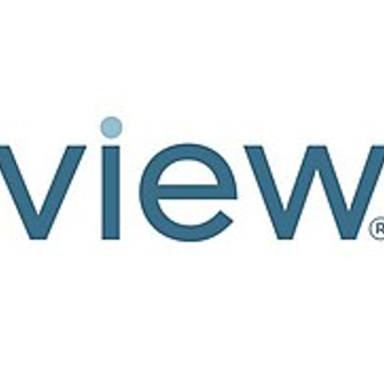
View
View is a Californian start-up that has created a glass solution that increases and optimizes the amount of natural light in buildings while simultaneously improving energy efficiency, and advancing smart and connected buildings.
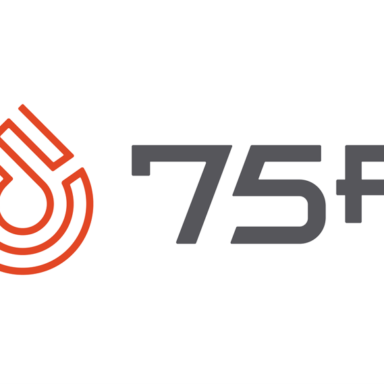
75 Fahrenheit
75F is a US-based start-up making smart building automation affordable and easy to deploy. 75F leverages IoT, Cloud Computing and Machine Learning for data-driven building intelligence and controls for HVAC, lighting and energy optimization.
123Fab #21
1 topic, 2 key figures, 3 startups to draw inspiration from

Low-carbon materials: a necessary transition in the construction industry
“The state of the building stock in Europe will make or break the European Green Deal”, said Adrian Joyce, Secretary General of the European Alliance of Companies for Energy Efficiency in Buildings. Indeed, buildings account for 19% of global greenhouse gases (GHG) emissions.
Construction materials account for 40% of the CO2 from buildings. This is due to 2 main factors: the overexploitation of raw material resources and/or the exploitation of polluting resources and the extensive use of energy-intensive components during their production phase. Cement is one of the main construction materials along with steel and accounts for 8% of the global CO2 emissions, which leads to the exploration for sustainable building materials. Low-carbon materials such as carbon concrete or wood fiber are a promising alternative. They are made using a waste-free production process and an energy and carbon-efficient production, assembly and transportation process.
Different technologies are being tested and developed:
- Short- and medium-term solutions: recycling and carbon compensation. An example of recycled industrial waste is high-density blocks which are made up of a mixture of lime fly ash and stone crusher dust. However, the cost and effort to recycle these materials remains high. Carbon capture solutions are also another way to decarbonize materials. Although this technology is premature today and not yet economically proven, it can capture carbon dioxide waste and prevent it from escaping into the atmosphere.
- Long-term solutions: substitution by new low-carbon materials. Low-carbon concrete appears to be a good way forward, as concrete will remain the most widely used building material in the coming years. Decarbonization of concrete means decarbonization of cement. Cement containing a high volume of one or more complementary cementing materials (CCM) (such as coal fly ash, granulated slag, silica fume and reactive rice-husk ash) is a promising alternative to clinker for reducing CO2 emissions. Extensive R&D is underway to use CCM in cement in Portland, and studies highlight that it could reduce greenhouse gas emissions in the global cement production by up to 80%. Many startups (e.g. CarbonCure, Carbon Clean Solutions, LanzaTech) are positioning themselves on this segment.
- Another alternative is bio-based materials. They are made up from substances derived from living organisms and can be used in many applications in the construction sector such as for insulation (vegetable fiber wools, straw bales, etc.). Some technologies create a material directly by mixing and compacting different bio-material parts (wood fiber, beams, posts, etc.), while others add customer polymer to the wood and plant fiber to make the material more resistant. However, there is still some reluctance towards bio-based materials, as they have not been shown to be comparable to their traditional counterparts (performance, ease of use, cost, etc.).
Although low-carbon alternatives are growing, there are significant barriers to their adoption, which explains why concrete and other high polluting materials are still widely used:
- The reluctance of major players to change: the key manufacturers who dominate the materials industry are slow to experiment or change business models. Architects, engineers, contractors, and clients are also cautious about the use of new building materials.
- Technical considerations related to the low-carbon transition: technologies such as carbon capture, use and storage, or the production of hydrogen-based metallurgical processes, have been demonstrated but are not yet commercially available.
- Cost of investing in new, low-carbon technologies and processes: the investment required for heavy industries, such as steel and cement, could be up to 60% higher than current levels.
Low-carbon materials still have a long way to go before they become a mature market, but there is reason for optimism. The transition to a low-carbon materials industry will be supported next year by the launch of a platform on the London Metal Exchange for the trading of low-carbon aluminium, mostly produced with renewable energy. This is the first time a metal will be traded based on its environmental footprint in the exchange’s 143-year history.
2 Key Figures
112 low-carbon materials startups
in the world
Market size expected to reach $377bn by 2022
According to Allied Market Research, the global low-carbon building materials market size was valued at $171bn in 2015 and is expected to reach $377bn by 2022.
3 startups to draw inspiration from
This week, we identified three startups that we can draw inspiration from: Carbon Clean, Woodoo and Kenoteq.
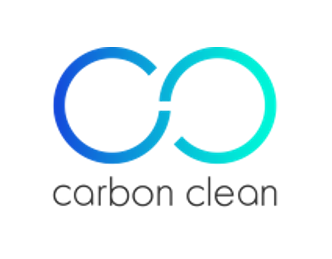
Carbon Clean
Based in London, Carbon Clean Solutions (CCS) provide carbon dioxide (CO2) separation technologies used for industrial and gas treating applications.
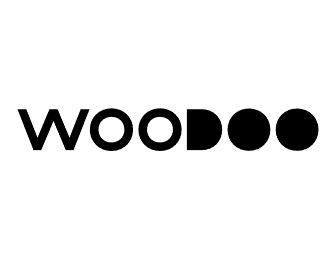
Woodoo
Based in Paris, Woodoo’s technology offers a second life to low-grade wood by transforming it through green processes into a waterproof, fire-resistant and highly performative material.
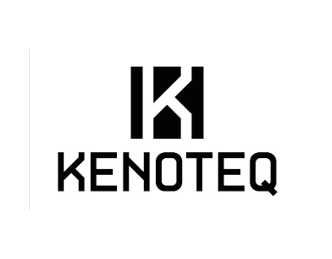
Kenoteq
Based in the UK, Kenoteq offers an unfired building eco-brick, K-Briq, made from 90% recycled construction materials and demolition waste.
123Fab #17
1 topic, 2 key figures, 3 startups to draw inspiration from
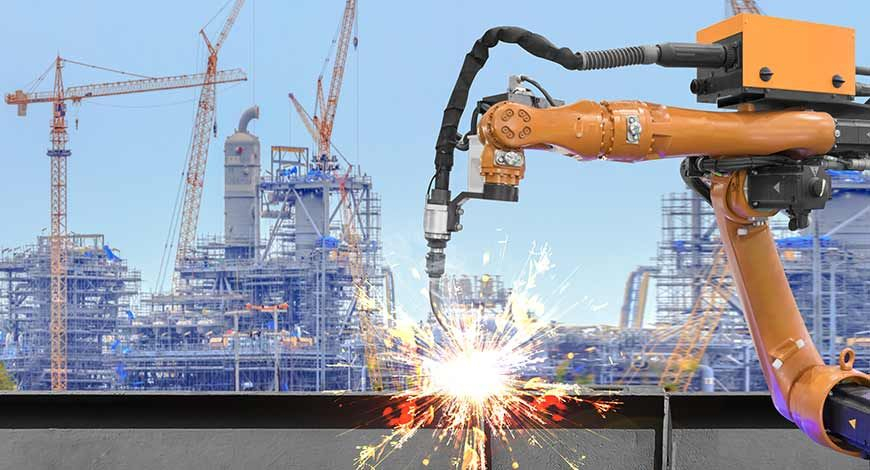
The slow adoption of robotics in Construction
Back in 1987, Japanese academics, robot manufacturers and contractors were already working on the first documented research about automated construction processes. Since then, construction robotics never stopped improving. ‘Robotics’ refers to the use of machines that have an automated component: construction robots are designed to help and assist humans in their day-to-day work on construction sites. The most common construction robots are stand-alone, fixed machines used for repetitive and precise applications (e.g. articulated arms). Then, there are collaborative robots (or cobots) that directly interact with human workers and perform a specific task – such as lifting heavy loads. A third type of robots are exoskeletons which are connected to the human body to support them in difficult tasks (e.g. for heavy-duty). Finally, the autonomous guided vehicles and autonomous mobile robots can navigate either onboard (e.g. camera or laser based) or in external environments (e.g. drones).
A good example of cobot is SAM (Semi-Automated Mason), the bricklaying robot designed by Construction Robotics. SAM works alongside the mason and assists him/her with the repetitive and arduous lifting and placing of bricks. The mason remains in charge of the setup and responsible for final quality. SAMs can lay 250 to 300 bricks per hour, improving by up to 4 times the number of bricks than a man could lay when working alone. With a retail price of $500,000, the firm that SAMs users can expect an ROI within three years, thanks to a reduction of labor costs by at least 30%, low maintenance costs and an expected lifespan of about 10 years.
Construction Robotics are not the only ones coming with an attractive value proposition for construction firms. Robotics companies and start-ups put forward financial benefits, productivity gain and safety as the main commercial arguments. Indeed, labor costs usually represent between 20% and 50% of a construction project total cost – and 38% of it could be automated according to a McKinsey study, leading to a potential cost saving of 20%. Although the initial investment is high, robotics firms claim that in the long-term, it is more cost-effective to purchase robots: in the United States, the average robot cost (including maintenance) is 4 times lower than labor wage stated McKinsey. Moreover, robotics is a guarantee of accuracy. Its work is extremely precise and predictable, thus meeting deadlines and avoiding delay expenses is easier. Another advantage of robotics is the minimization of injuries and providing a safer workplace. For instance, autonomous vehicles can operate independently in hazardous areas.
However, robotics in construction is still not widely adopted and there is under-automated when compared to other manufacturing industries. The construction industry has been classified by McKinsey as « in middle range for automation ». There are several reasons for slow adoption rate of robotics in this industry:
- The complexity of construction sites – unique end-product, unpredictable weather – leads to non-repetitive tasks and involving judgement
- The unpredictable and ever-changing environment: the flexibility required for construction works is for still difficult to automate. As previously said, only 38% of the time spent on unpredictable physical work in construction could be automated with current technologies compared to a 70% for predictable physical work (e.g. in automotive).
- The need for technology to improve: although there are plenty of promising innovations, improvements of the current technology are needed in the adaptability to real-time variability. Moreover, on construction sites there are hundreds of tasks and multiple phases. As there is no multitask-programmed robot, many construction firms remain reluctant to integrate robots to their regular activities.
- The significant investment costs: Investing in robotics involves high initial capital investment, including R&D. Although in the long term it is said to be beneficial, it remains an obstacle for many companies.
- Legal and safety issues: even though robots should reduce the risks on construction sites, the appropriate allocation of risk is a concern for all the construction participants. There is a need specific regulation in the use of robotics on sites. This issue is starting to be addressed (e.g. the compulsory use of Building Information Models in UK since 2019). The cyber risk also needs to be considered.
- Jobs implications: If 40% of current construction jobs would be “at high risk” of automation by the 2030s, according to a 2018 PwC study, the transition will take some time and the major challenge for workers will be to not be replaced by robots but to learn to work side by side with them. A specificity of the construction industry is the importance of craftsmanship, that adds value to projects. Replacing all human workers by robots would mean taking away the quality-assessment aspect that current robots cannot provide. Thus, collaborative robots may be the most appropriate solution as they are designed to work alongside human counterparts instead of entirely replacing them. Cobots will contribute to improve productivity by carrying out tasks that would otherwise be considered busywork or for employees.
The current labor-shortage in construction – A 2019 survey by Associated General Contractors of America and AutoDesk reported that 80% of firms find it difficult to hire labor force – will surely weight into the scale of construction robotics rise. Thanks to 5G and other technology improvements, better connectivity will make it easier for multiple robots to co-operate and better understand the environment they are operating in. Compared to other heavy industries, job automation in construction is rather low but it is poised to increase faster than them in the coming decades. According to a PwC study, in the late 2020s, job automation potential in construction is 16% versus 19% on average for all industry sectors but the automation potential for construction in the mid-2030s is forecast to be 39% versus 30% for all sectors.
2 Key Figures
77 construction robotics startups
in the world, according to a Tracxn query.
Market size expected to reach $460M by 2026
According to Verified Market Research, the global Construction Robotics market size was valued at $212 Million in 2019 and is expected to reach $460 Million by 2026.
3 startups to draw inspiration from
This week, we identified three startups that we can draw inspiration from: Construction Robotics, Kewazo and SuitX.
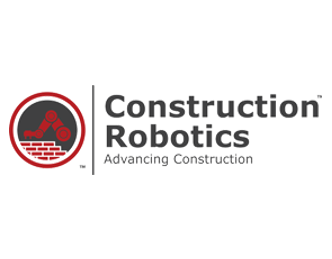
Construction Robotics
New-York based company, Construction Robotics is dedicated to developing affordable, leading-edge robotics and automation equipment for the construction industry.
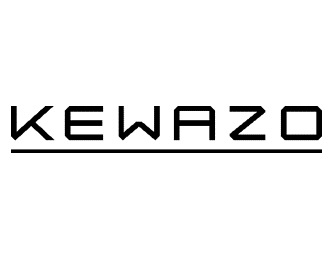
Kewazo
Based in Munich, Kewazo develops smart robotic elevators for industrial and construction sites with focus on scaffolding. Kewazo solutions intend to improve construction logistics via data analysis and robotics.
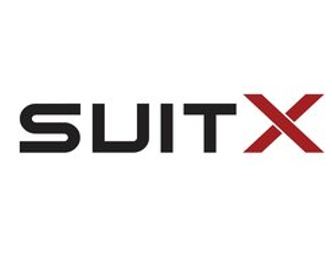
SuitX
The US-based startup SuitX builds a robotic exoskeleton for medical and industrial markets, designed to reduce the amount of strain on the knees and quadriceps.