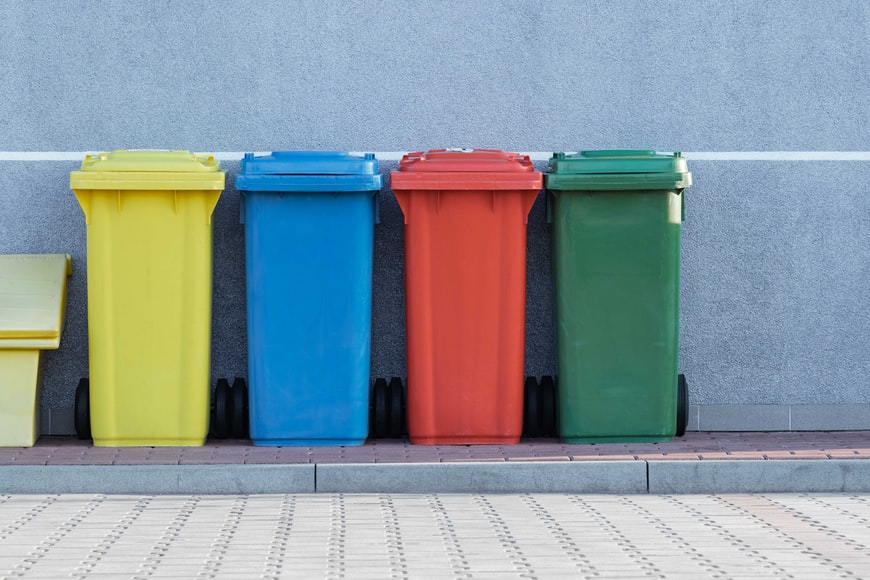
In 2021, the circular economy became the most funded sector in private equity, with over €2.2 billion invested, almost double the previous year (Novethic). Back Market, the electronics reconditioning specialist, has made this rise possible with €726 million in two rounds of financing. The model is gradually proving its cost-effectiveness and is of increasing interest to consumers who are turning to much more frugal lifestyles and consumption patterns.
The circular economy consists in producing in a sustainable way by limiting consumption and the production of waste. It can be defined more broadly as a system that valorizes resources at each stage of their transformation. The resources can be raw materials, finished products, goods, or services (such as car-sharing). According to ADEME, the French Environment and Energy Management Agency, the functioning of this system is based on 7 pillars: sustainable supply of raw materials, eco-design of products, industrial and territorial ecological commitment, ecology of functionality, responsible consumption of products, extension of the useful life of goods and recycling of materials from products. The shift of companies from the linear to the circular model has advantages and challenges on several levels. From an economic point of view, the model allows companies to save on the costs of acquiring and transporting raw materials, which are abundantly available. This model is also a strong asset for companies as it improves their brand image and appeals to the growing number of environmentally conscious consumers. In addition, the circular economy is becoming more and more popular to comply with the increasingly strict regulations of the States in favor of ecology: the display of the lifespan of products, the development of packaging deposits, the support of the economy of functionality or the fight against waste and programmed obsolescence. In line with its March 2020 Circular Economy Action Plan, the European Commission last month presented proposals to green almost all physical goods on the EU market, with for example the introduction of ‘digital passports‘ for relevant products and ‘performance classes‘ from A to G for comparison.
Nevertheless, the circular economy model requires certain key success factors to establish effectively and sustainably. Firstly, the model must continue to prove its capacity to improve the profitability of industries, particularly those in emerging countries, which still have significant development potential in the linear model. Secondly, manufacturers need to have access to their products at the end of the cycle. Information technology can partly address this concern with for example online failure detection or monitoring of wear levels. From a macro-economic point of view, an ecosystem should enable actors to work together, facilitating shared objectives, dialogue, and alliance, sometimes even with competitors. Another important criterion is the establishment of reverse logistics channels to collect and optimally recover the considerable end-of-cycle volumes generated by the circular economy. Industrialists will be directly concerned, particularly for closed loops, but also SSE (social and solidarity economy) players and local authorities.
To this extent, several startups and large groups are developing solutions and initiatives to benefit from circular economy. A distinction can be made between operators, who try to modify their production processes and limit waste production, and companies that offer solutions to facilitate the circular economy, in terms of logistics, product monitoring, quality assessment, etc. In textiles, some large players such as Patagonia have focused on a strategic positioning allowing access to products at the end of the cycle with the presence of an “absolute guarantee” allowing the repair and modification of its articles. External startups, such as Murfy, are also choosing to penetrate this part of the value chain by encouraging consumers to repair household appliances rather than replace them with new ones. It offers three services: free tutorials on how to repair household appliances, repair by an employee technician, and an e-commerce platform for reconditioned appliances. Intending to create a circular economy ecosystem, another startup, Phenix, offers a range of solutions to companies – supermarkets, local shops, but also producers, industrialists, and wholesalers – to give a “second life” to their unsold goods, by putting them in touch with second life item collectors (charitable associations or even sales at a reduced price through a mobile app). The startup saves 120,000 meals a day, thus avoiding the production of 50 tons of waste per day. Finally, in a more global logic of recycling, several startups have contributed to the creation of the “internet of garbage“. This is the case of AMP Robotics, which raised 55 million last year and uses AI and physical robots to orchestrate sorting, picking, and placement tasks to increase recycling rates.
The circular economy holds great promise for the future. It is of increasing interest to companies in all sectors notably to reduce production costs and ensure an abundance of raw materials. It is also increasingly important for their image in the eyes of consumers who want to consume sensibly and sustainably. Finally, it is the subject of particular attention from the public authorities, who are enacting laws to act in favor of the environment and limit the production of waste.
2 Key Figures
Circular economy revenues in the plastic packaging recycling market are expected to have a CAGR of 9.1% between 2019 and 2030
The market revenue is estimated at $13.1 billion – Research And Markets
750 funded companies & + $3B invested in last 2 years in circular economy
Traxcn
3 startups to draw inspiration from
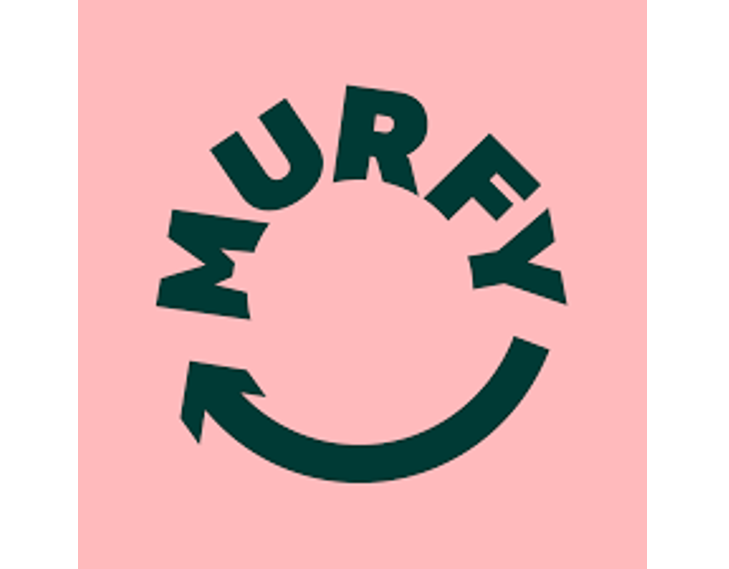
Murfy
Murfy, created in 2017, has undertaken the mission of solving the overconsumption of household appliances, via the circular economy. It thus offers three services: free tutorials to repair one’s own household appliances, repair by an employed technician, and an e-commerce platform for reconditioned appliances. In one year, Murfy has tripled its turnover to €3.5 million in 2020.
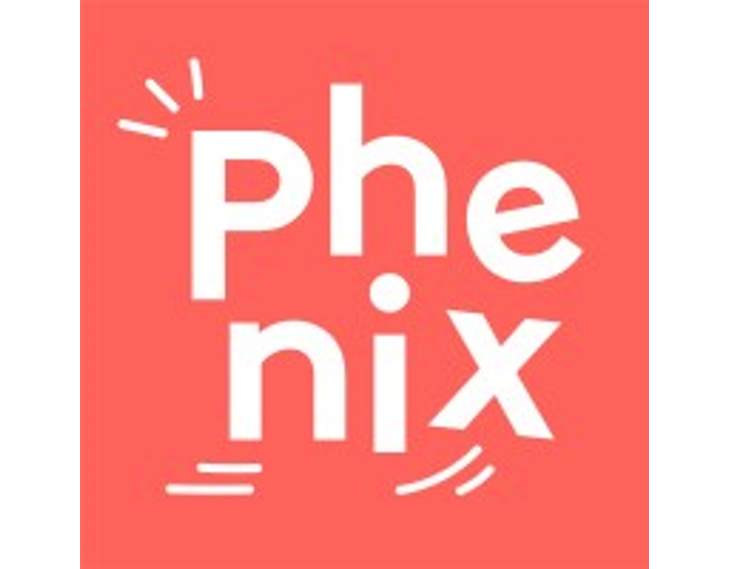
Phenix
Phenix has developed a platform to connect generators and collectors of second life items. The platform, Phenix Exchange, connects waste generators, ie companies and industries that want to sell off their old items, to agencies that wish to buy these items. These include recycling companies, NGOs etc. The startup raised $17,2M in 2018.
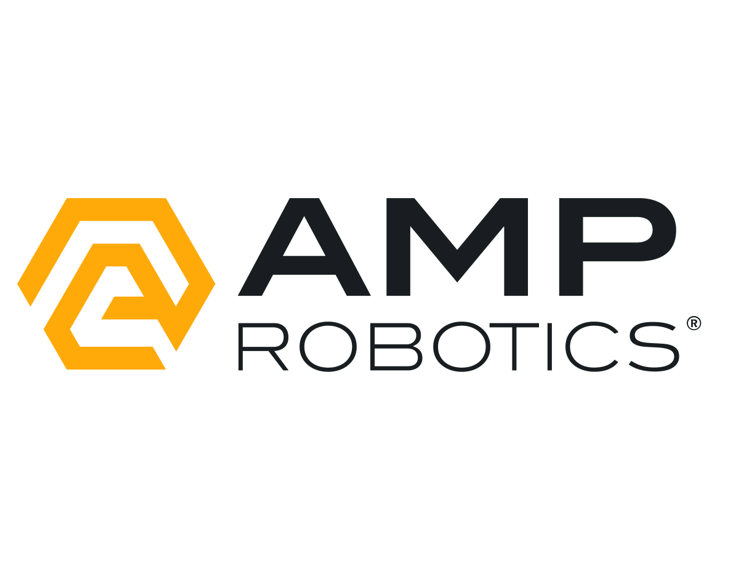
Centrical
The American startup has developed an artificial intelligence-based waste sorting robot which picks recyclable materials off a conveyor belt in mixed waste, construction & demolition waste, and e-waste facilities. AI-technology is used to identify the waste material and machine learning platform keeps record of types of materials identified. The startup raised $55M in 2020.
Interested in a startup landscape or in an insights report?
Please fill out our contact form so that we can get back to you very quickly with our product offer.
Want to subscribe to our 123Fab?
Fill out our form to receive the latest insights into your inbox.
123Fab #74
1 topic, 2 key figures, 3 startups to draw inspiration from
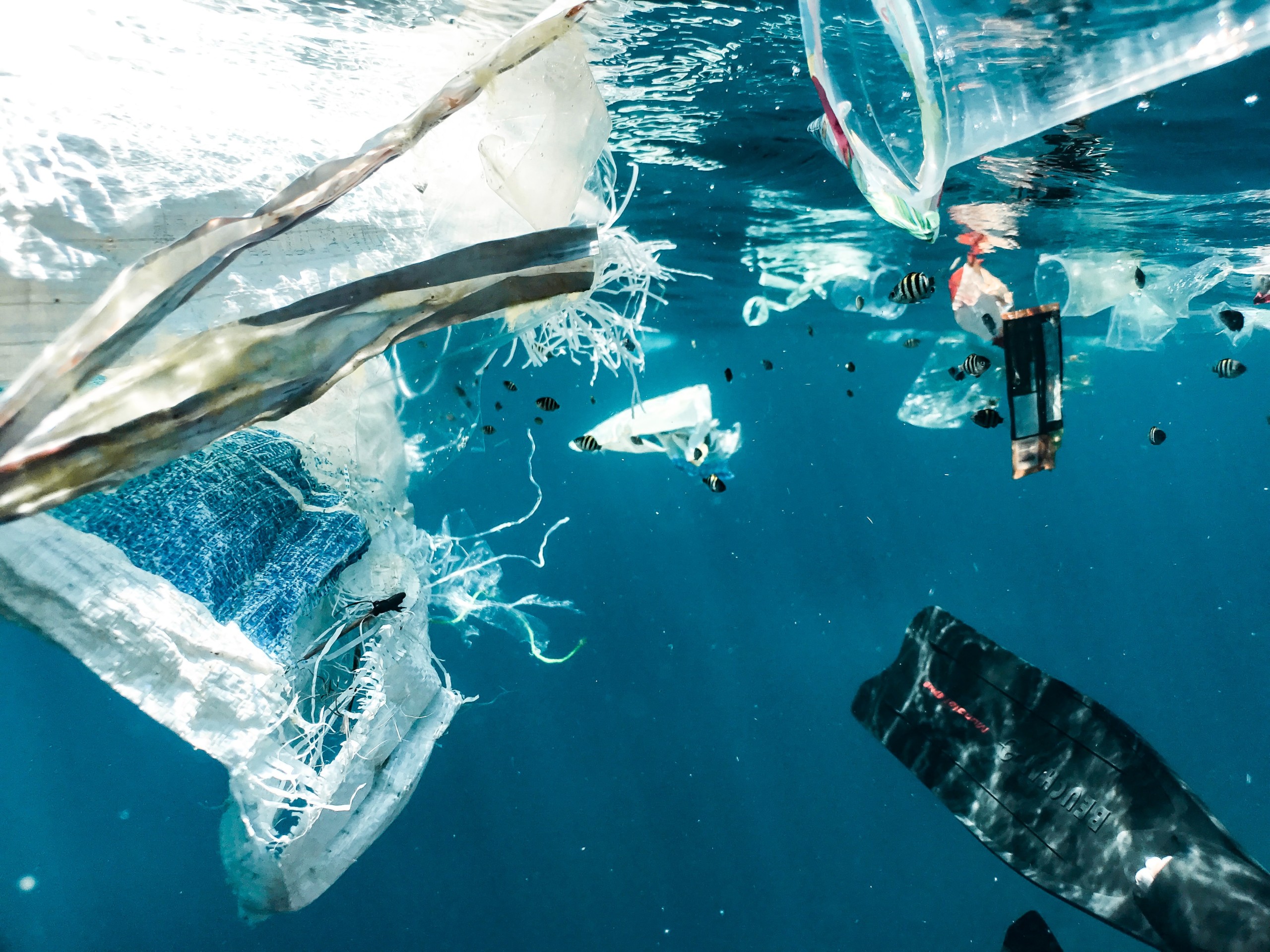
Plastic pollution in oceans is one of the most pressing environmental issues. The Great Pacific garbage patch alone is estimated to be 1.6 million square kilometers wide, three times the size of France, and contains about 1.8 trillion pieces of plastic, the equivalent of 250 bits for every human being. Once in the ocean, the sunlight, waves, and wind break the plastic into increasingly smaller pieces, ultimately reaching the size of microplastic (<5mm) which are then dispersed in the water. This affects all marine organisms since their small size makes them virtually impossible to collect once they have broken down. Some companies have decided to tackle the problem by collecting and upcycling these plastics in order to slow the growth of these garbage continents but NGOs remain the key players in the sector. As recycled plastics cannot financially compete with cheap new plastics, it is hard for startups to identify a clear business model.
The Ocean Cleanup is a non-profit organization based in the Netherlands that aims to remove 90% of floating ocean plastic. It harvests it by dragging a 3-meter deep, 800-meter long net between boats throughout the Pacific garbage patch. To make the capture as efficient as possible, they use computational modeling to predict where the highest concentration of plastic is. However, one of the problems with this technology is that the surface to be covered to retrieve plastics in the ocean is gigantic. Luckily, most plastic in the ocean arrives via rivers, which is easier to filter. Thus, they place barriers on rivers to guide floating plastic to solar-powered conveyor belts that carry it to dumpsters. As for River Cleaning, they place floating devices diagonally across the river to form a chain to a storage area on the riverbank. The river current makes the devices spin so that floating plastic is diverted from one device to the other to end up in the storage area. One highlight of this solution is that, as each floating device is anchored to the bottom of the river, they allow ships and boats to pass through and return to their position by themselves. Another innovative technology to filter plastics from rivers is provided by The Great Bubble Barrier, pumping compressed ambient air through perforated tubes at the bottom of the waterway to create a diagonal bubble curtain that will direct plastics to the storage area on the side of the river. The bubble curtain is also safe for fish and ships traffic and increases the oxygen concentration in the water, benefitting the aquatic ecosystem.
The main obstacle to these technologies is that sorting and recycling the different types of plastic is expensive, while the plastic itself is cheap. Some companies have focused on revalorizing the plastic in the ocean. Bureo partners with fishermen to retrieve discarded fishing nets, which represent more than 46% of the great pacific garbage patch and transform them into their NetPlus material that can then be used to make clothes, skateboards, sunglasses, or even board games. Oceanworks also provides materials such as resins, textiles, bottles, and more made from recycled plastics collected by local communities throughout the world. The retrieved plastics come either from the ocean, streams, and waterways or coastal areas. Oceanplastik, meanwhile, plans to create an ecosystem based on crypto tokens to reward the collection of plastic waste before it reaches the ocean. Their phone app would allow users to tag, collect and drop off plastic wastes at collection points and earn crypto tokens. The recovered plastics would then be sorted, washed, and recycled into granules to use in new plastic products.
Major industrials are interested in recycled plastic from the ocean, like Patagonia’s partnership with Burneo to use their recycled fishing net as fabric for their clothes. Last year, Coca Cola announced a partnership with The Ocean Cleanup to support the deployment of their solution on 15 new rivers by the end of the year. In 2020, the world’s largest zipper manufacturer YKK partnered with OceanWorks to produce an ocean-sourced collection of zippers.
As humanity has just crossed the 5th planetary limit on chemical pollution, in which plastic production plays a major role, recycling and collecting plastic waste is more important than ever. However, it goes without saying that limiting its production and use remains a mandatory step toward a sustainable future. Startups like Notpla and Sulapac are good examples of the role startups can play in avoiding single-use plastics in packaging and helping to keep our ocean clean.
2 Key Figures
37 Ocean cleaning initiatives
Registered by Tracxn
By 2040, a total of 600 metric tons of plastics could be accumulated in the seas
Compared to 150 metric tons in 2015 – National Geographic
3 startups to draw inspiration from
This week, we identified three startups that we can draw inspiration from: River Cleaning, The Great Bubble Barrier and Bureo.
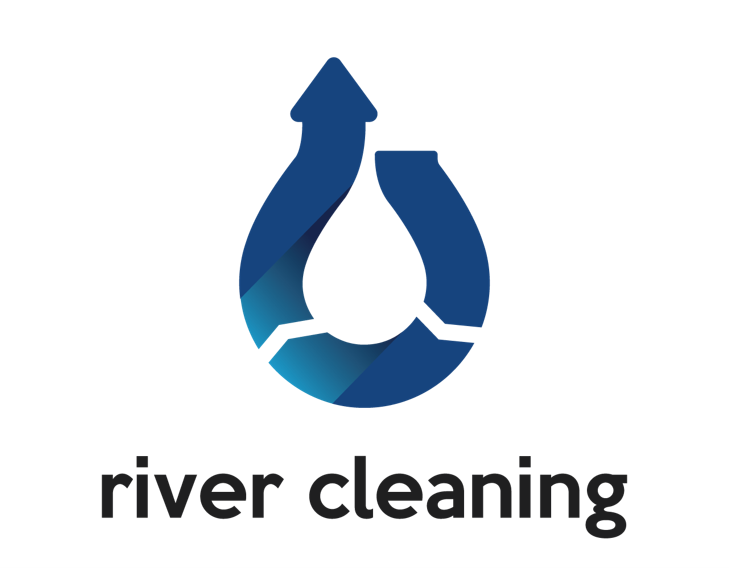
River Cleaning
The Italy-based startup River Cleaning produces and install cleaning system made up of a series of floating devices, positioned diagonally on the course of the river; thus positioned, they allow to intercept plastic waste and transport it to the river bank, in a special storage area.
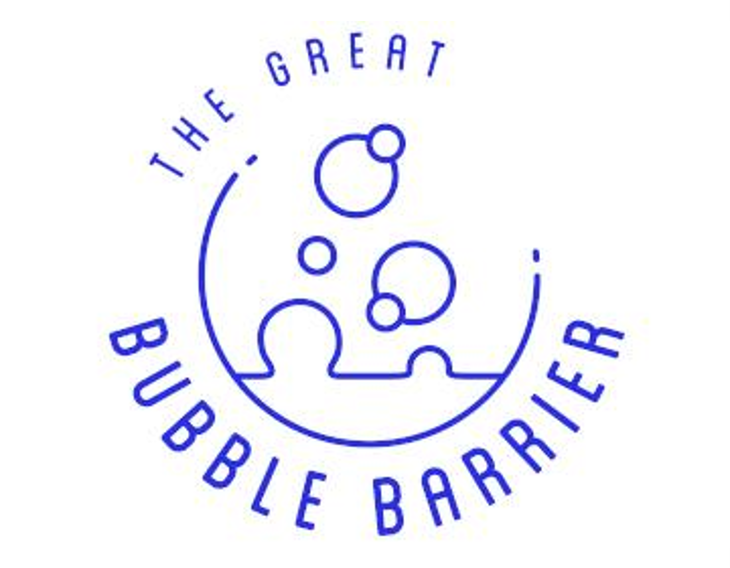
The Great Bubble Barrier
Founded in 2017 in the Netherlands, The Great Bubble Barrier developed a bubble barrier designed to stop plastic pollution in rivers and canals. Their barrier is comprised of bubble curtain, compressor, and catchment system, enabling users to collect and remove plastics from waterways.
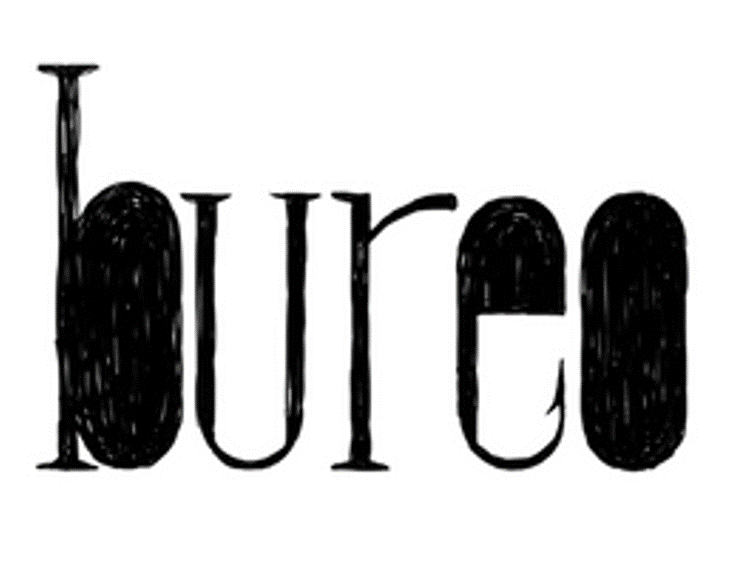
Bureo
Manufacturer of plastic goods designed to sell materials made from ocean waste, specifically from nylon fishing nets. Bureo produces and sells sustainable skateboards, sunglasses, t-shirts, and caps made from recycled fishing nets, enabling consumers to protect the environment around them, using innovation to inspire change and create tangible positive impacts.
Interested in a startup landscape or in an insights report?
Please fill out our contact form so that we can get back to you very quickly with our product offer.
Want to subscribe to our 123Fab?
Fill out our form to receive the latest insights into your inbox.
123Fab #64
1 topic, 2 key figures, 3 startups to draw inspiration from
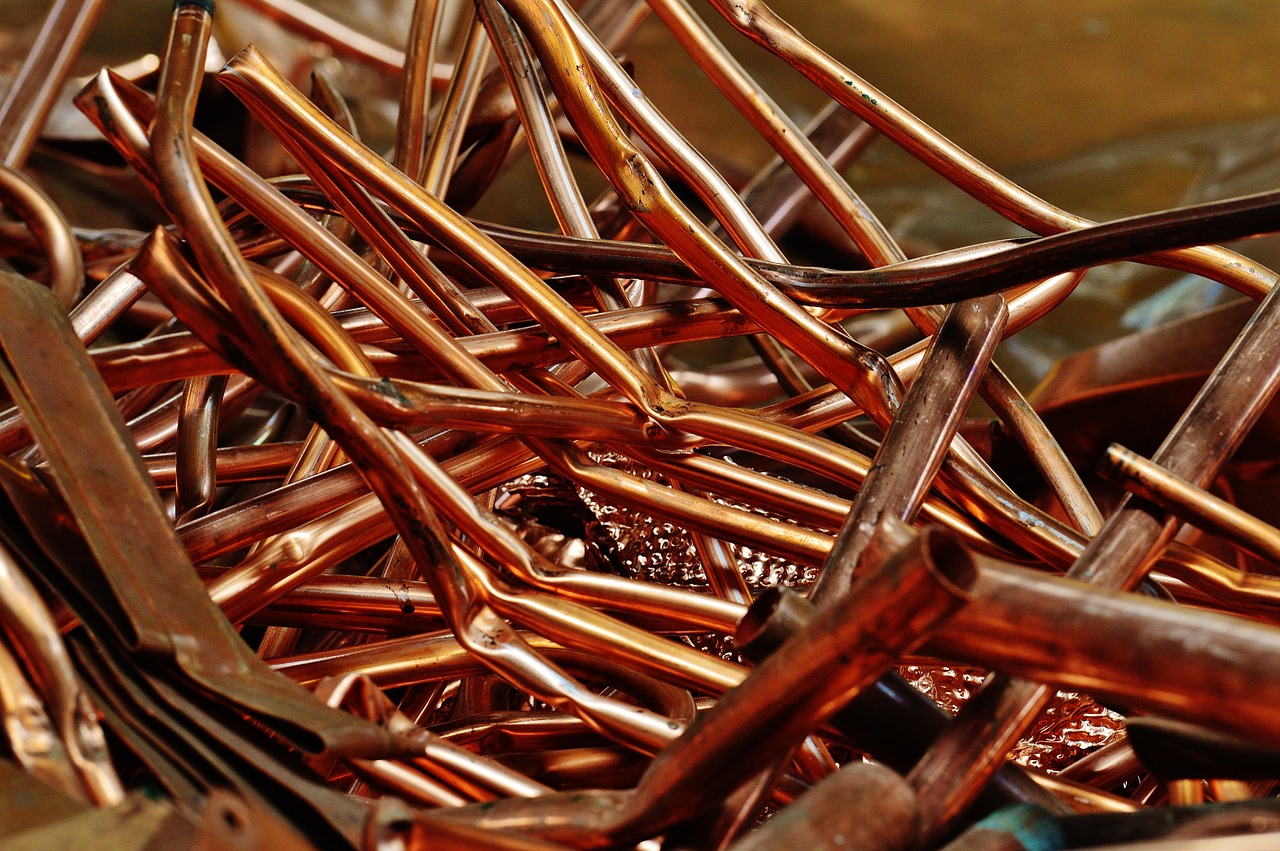
Copper plays a major role in the global economy. From thermal and electrical conductivity to corrosion resistance, copper is an extremely versatile metal that has long contributed to the way the world works. By way of illustration, it is used in numerous industries such as telecommunications (cables, wires), electronics (printed circuits, chips), transportation (injection systems, braking circuits), construction (pipes, tubing), currency, etc. In fact, one tonne of copper brings functionality to 40 cars, powers 100,000 mobile phones, runs 400 computers and distributes electricity to 30 homes.
This year, the price of copper broke the $10,000 per ton mark for the first time in 10 years. This indicates an expected increase in global demand, which should benefit Chile, Peru and China (47% of global production). Described as the ‘new oil’, demand for copper has been driven in recent years by its vital role in a number of rapidly growing industries, such as electric vehicle batteries and semiconductor wiring. According to Citigroup Global Markets, demand related to renewable power generation, battery storage, electric vehicles, charging stations and related grid infrastructure accounts for about 20% of copper consumption. Thus, copper is lauded as an essential, structural metal for the energy transition. However, the recent price surge threatens to make decarbonization more costly. At the same time, the global average copper ore grade is expected to decrease, as mines with higher ore grades become exhausted. As a result, there is growing concern about the availability of copper, and several studies have sought to estimate the peak of global copper production using Hubbert’s model, which has been estimated to be between 8 and 40 years from now.
Given the importance of copper, innovation is beginning to spur in the industry. Continuous research and testing of new concepts are being deployed to make processes more efficient, minimize environmental impact, lower energy consumption and improve design. In 2015, Aurus III, a $65 million venture fund focused solely on copper mining innovation, was launched in Chile. Among the startups they have invested in are Ceibo (formerly known as Aguamarina), which focuses on soil stabilization through biomineralization, and Scarab Recovery Technologies, which is centered on recovering valuable materials from tailings. Recycling is also receiving increased interest because copper – like gold, silver and other non-ferrous metals – suffers no loss in quality from the process, making it infinitely repeatable. In addition, it requires up to 85% less energy than primary production. Hamburg-based Aurubis is one of the companies leading the charge on the recycling of copper and other metals by a pyrometallurgy method. This year it announced that it is investing €27 million in a new recycling plant at its Beerse country site. The ASPA plant will process anode sludge, a valuable intermediate product from the electrolytic refining of copper, from the recycling sites in Beerse and Lünen, Germany. New Zealand startup Mint Innovation, however, uses a unique biohydrometallurgy method. Launched in 2016, it has developed a low-cost biotech process to recover precious metals from e-waste. It raised NZ$20 million last year to build its first two biorefineries in Sydney, Australia and northwest England.
It should be noted, however, that the copper recycling business requires considerable financial resources, particularly in terms of working capital and cash flow. This is what led to the near bankruptcy and takeover of the French factory M.Lego, which employs 110 people. Likewise, while secondary production of refined copper has increased in volume and percentage, it is growing at a much slower rate than the waste stockpile. This is primarily due to the fact that the sectors with the highest recycling rates (construction and infrastructure) have their copper tied up for several decades due to the life of the structures built. In contrast, consumer goods, which have a shorter life span, are only recycled at rates between 25 and 40%
In short, copper is projected to be a critical metal in the coming years, with a vital role to play in the energy transition. The gradual depletion of its reserves and dependence on certain countries is driving companies to innovate in the field of recycling, in order to make it both more profitable and sustainable. However, the copper industry will need strong government support to stimulate innovation to avoid a gradual shortage that would contribute to a sharp increase in prices.
2 Key Figures
About 50% of the copper used in Europe comes from recycling
International Copper Study Group (ICSG)
Copper consumption is predicted to rise more than 40% by 2035 compared to 2018
European Copper Institute (2018)
3 startups to draw inspiration from
This week, we identified three startups that we can draw inspiration from: Mint Innovation, Sortera Alloys and Weeecycling.
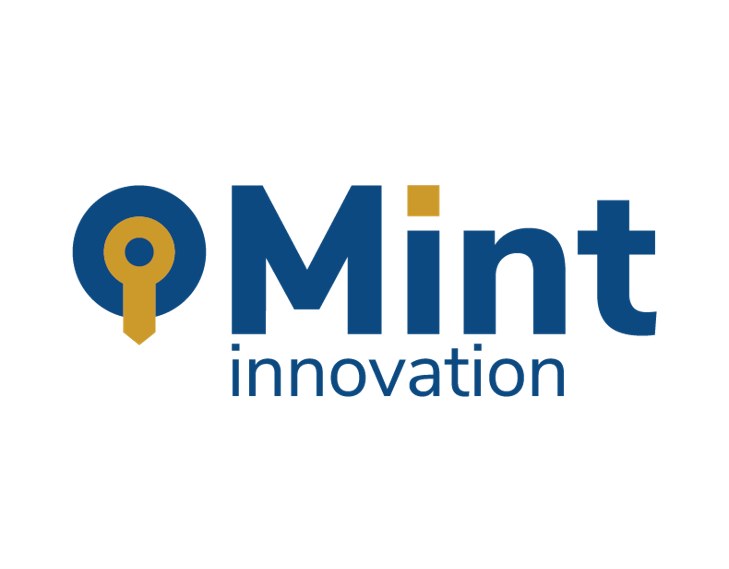
Mint Innovation
The New-Zealand startup has scaled biological processes that recover valuable metals like copper from electronic waste and other residues. The company’s firm uses microbes to selectively and rapidly recover precious metals from various low concentration materials under environmentally benign conditions.
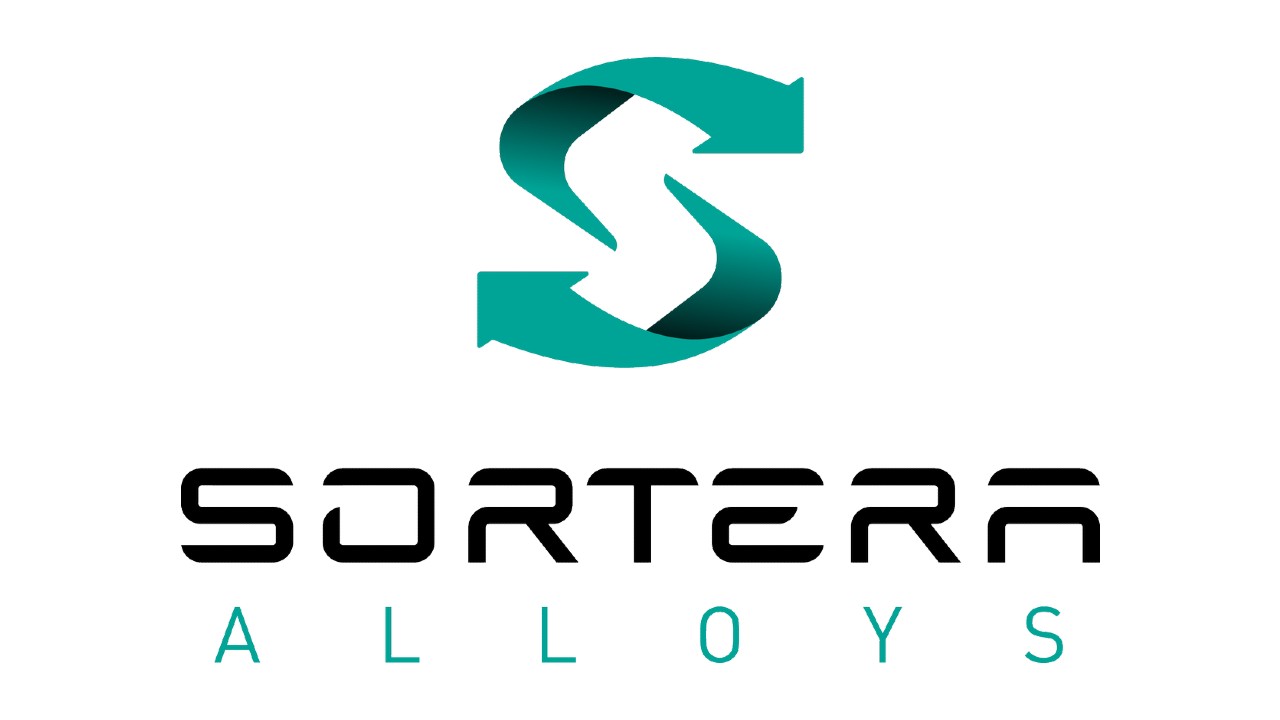
Sortera Alloys
The American startup has developed a sorting system designed to reuse metals recovered from end-of-life products. The company’s system sorts metal by its type and alloy composition through a combination of X-ray fluorescence and optical sensor fusion, artificial intelligence (AI) and machine learning image processing.
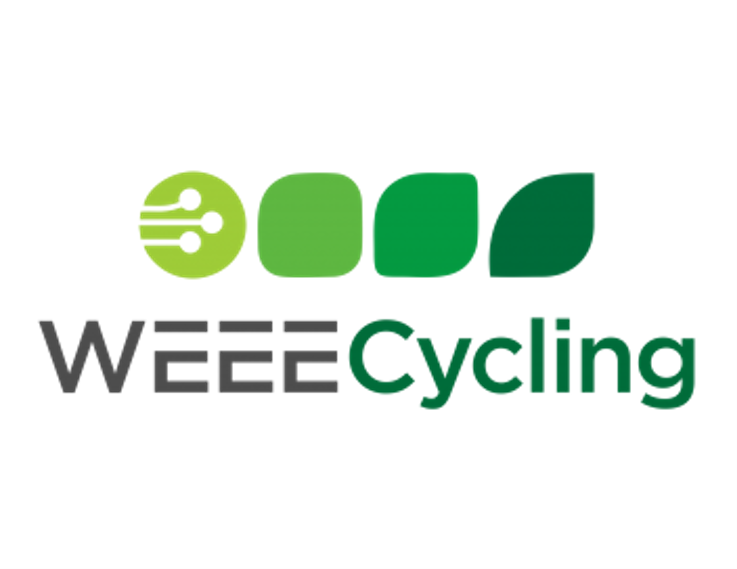
Weeecycling
The French startup WeeeCycling has set up a circular economy loop for recycling strategic metals. The company buys electrical and electronic scrap in the world and, via its Morphosis brand, manufactured products. The rare metals are then extracted through a thermal and electrochemical stage to be resold for reuse.
Interested in a startup landscape or in an insights report?
Please fill out our contact form so that we can get back to you very quickly with our product offer.
Want to subscribe to our 123Fab?
Fill out our form to receive the latest insights into your inbox.
123Fab #40
1 topic, 2 key figures, 3 startups to draw inspiration from
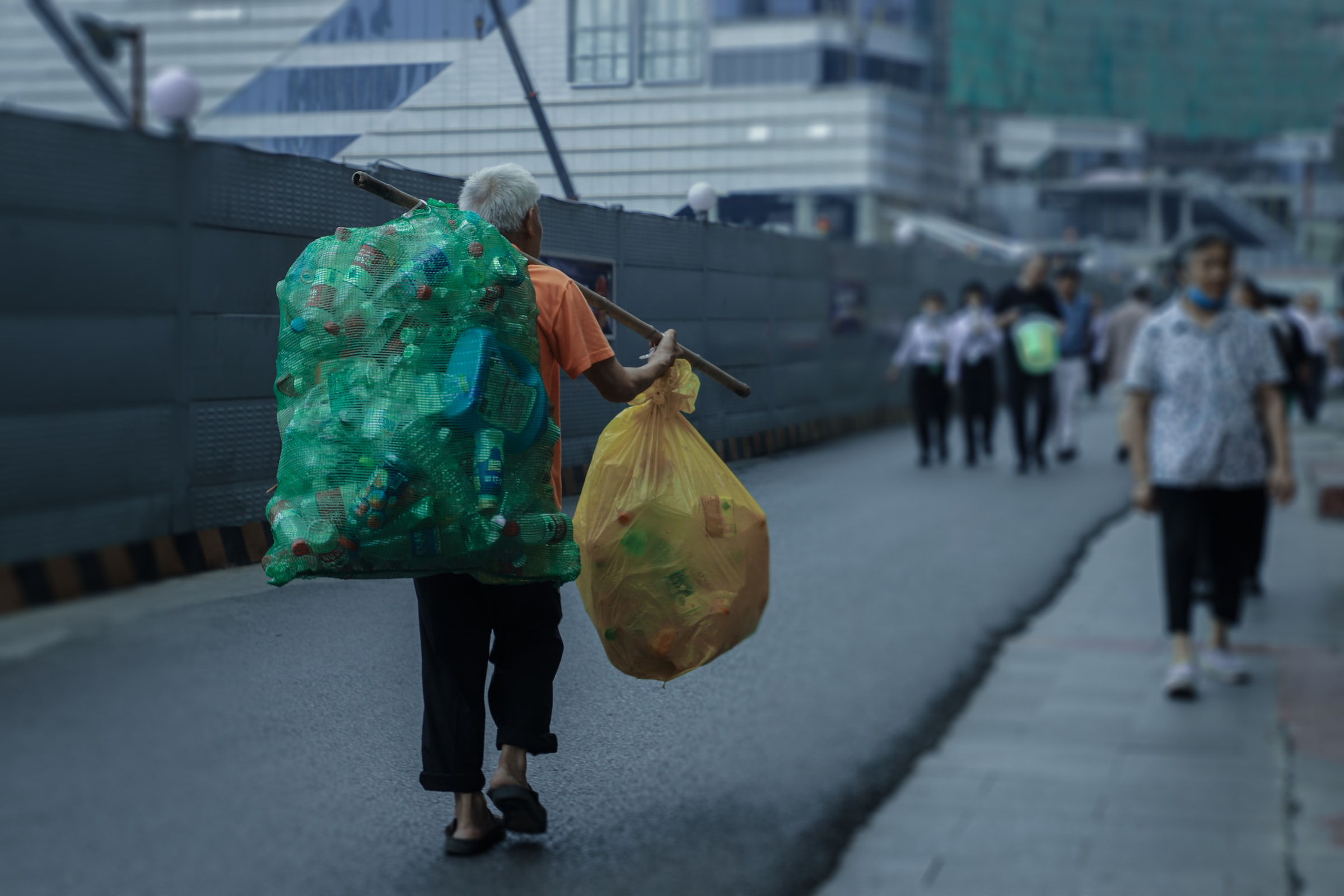
Plastic pollution is one of the most important environmental issues of the coming years. Plastic’s low cost and ease of production have made it an indispensable material in many sectors, especially in packaging, accounting for more than 45% of plastic waste generation in 2015. Due to its slow decomposition rate and the fact that 40% of all plastic trash is single-use, plastic waste has rapidly grown, making end-of-life management a burden for policymakers. Last year, France adopted an anti-waste law, setting a goal of 100% recycled plastic by 2025 and a ban on single-use plastic packaging by 2040. In 2015, 8% of plastic was incinerated, 7% was recycled and 55% was disposed of in landfills or the natural environment, while 30% was used. There are many types of plastics, from thermoplastics and thermosetting polymers to crystalline plastics and bioplastics, but the vast majority of plastics are made of polymers.
Today, the primary means of recycling is mechanical recycling, which accounts for more than 99% of infrastructure and business. The principle is simple, it involves crushing plastics into granulates, washing them and then melting them down so that they can then be reused. To be efficient, mechanical recycling requires a clean stream of plastic waste. Thus, thorough sorting needs to be done beforehand to separate plastics by color and type, which makes it impossible to recycle laminated packaging (made of different plastics). Mechanical recycling is also limited because plastic can only be recycled a maximum of 5 to 7 times, and be reused in low-value products, which calls into question the economic viability of this method.
In recent years, chemical recycling has gained momentum, with the goal of providing a solution for hard-to-recycle products and the potential for an infinite number of recycling cycles. Among the chemical recycling processes, depolymerization has attracted the most interest from startups and corporates.
What is depolymerization? Polymers are long associations of chemical entities called monomers. Depolymerization is the process of breaking the bonds of the polymer chains to create a mix of monomers. It is very useful for plastics because the products of this chemical reaction can then be reused.
To tackle the recycling problem, depolymerization of plastic waste can be used in various ways:
- From plastic to fuel: Some, such as CPD-Swiss or Paterson energy, depolymerize any type of plastic waste using pyrolysis (heating the material without oxygen) to create “pyrofuel”, or catalysis (accelerating the chemical reaction by introducing another chemical entity) to create synthetic diesel. Part of the fuel produced can then be re-used to produce heat in the process, making it energy self-sufficient, and the product can be used as an alternative fuel and energy carrier.
- Plastic to feedstock: Nexus fuel and Polycycl focus on some categories of plastics, HDPE, LDPE, PP, and PS (#2,4,5 and 6 in recycling codes), which are not recyclable with conventional methods and represent approximately 60% of the plastics on the market. They use depolymerization to turn them either into petrochemical feedstock or back into virgin plastic (purified plastic resin). The first through pyrolysis, the second through a proprietary chemical recycling technique called Contiflow Cracker. Plastic energy uses the same categories of plastic to produce syngas (used to make the plant run) and feedstock to re-create virgin plastic.
- Plastic to plastic: Some startups focus on recycling one type of plastic such as Pyrowave, which uses microwave-based depolymerization of polystyrene (#6 recycling code) to turn it into styrene, its associated monomer. This styrene can then be re-polymerized into polystyrene indefinitely. Ioniqa on the other hand focuses on PET (#1 recycling code). The company uses a smart fluid (a fluid whose properties can be changed by applying an electromagnetic field) to dissolve the polymers constituting the PET back into monomers, which can, in turn, be used to produce brand new PET. Both these startups aim to provide a new way to attain a truly circular use of these resources.
Corporations are also interested in depolymerization techniques. Four months ago, Shell announced a partnership with Nexus Fuels to scale-up commercial production of chemicals from plastic waste. At the end of 2018, Coca-Cola announced a partnership with Ioniqa to produce new bottles containing at least 50% of recycled PET by 2030, the same year PepsiCo announced a multi-year supply agreement with Loop Industries to produce 100% recycled PET containers using Loop’s depolymerization technology. Sealed Air, a leading packaging corporation, invested in Plastic Energy last year to enhance plastic recycling circularity.
Pre-treatment of plastic waste remains a key factor for recycling. Saperatec has chosen to address the problem of laminated packaging treatment by creating separating fluids that split the various layers of such packaging. The split products can then be re-used. In 2018, adhesive giant Henkel invested in Saperatec to form a collaboration to enrich its recyclable adhesive line.
Depolymerization seems to have gained a lot of momentum in recent years, but green groups are questioning the efficiency of these processes at scale and their environmental impact. Particularly with regard to the potential release of toxins during the processes and their energy intensity compared to mechanical recycling, as well as the carbon emissions entailed by the consumption of plastic-based fuels.
2 Key Figures
39 plastic recycling startups
registered by Crunchbase
Plastic recycling market expected to reach $60.7Bn by 2025
The global plastic recycling market was estimated at $42.3Bn in 2020 and is expected to reach $60.7Bn by 2025, growing at a CAGR of 7.5%.
3 startups to draw inspiration from
This week, we identified three startups that we can draw inspiration from: CPD-Swiss, Nexus Fuels, and Pyrowave.
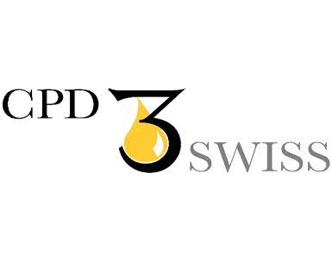
CPD-Swiss
CPD-Swiss is a Swiss-based startup created in 2012. It specialises in the development and implementation of projects for the production of diesel fuels and storable energy carriers from renewable residual waste materials (biomass) and from organic waste (plastic, synthetic materials, etc.). For this purpose, CPD-SWISS develops and builds industrial plants based on CPD technology (Catalytic Pressureless Depolymerization).
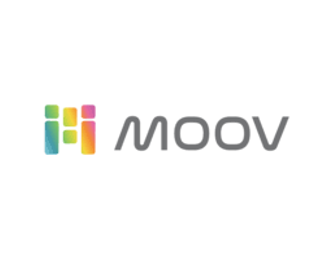
Nexus Fuels
Nexus Fuels is a startup based in Atlanta, provider of waste management services designed to convert waste plastics into plastic feedstocks and fuels. The company’s services reduce plastic waste from being landfilled and has low operating costs, enabling people to convert difficult-to-recycle waste plastics into fuel and virgin plastic.
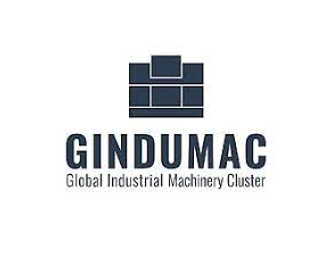
Gindumac
Based in Ontario, Pyrowave is the developer of a microwave-based chemical recycling technology intended to enable plastic regeneration. The company’s technology regenerates post-consumer plastics by breaking them down into intermediate products that are used to make plastics identical to virgin plastics, thereby enabling customers to reduce plastic waste and be a part of a circular plastic economy.
123Fab #38
1 topic, 2 key figures, 3 startups to draw inspiration from
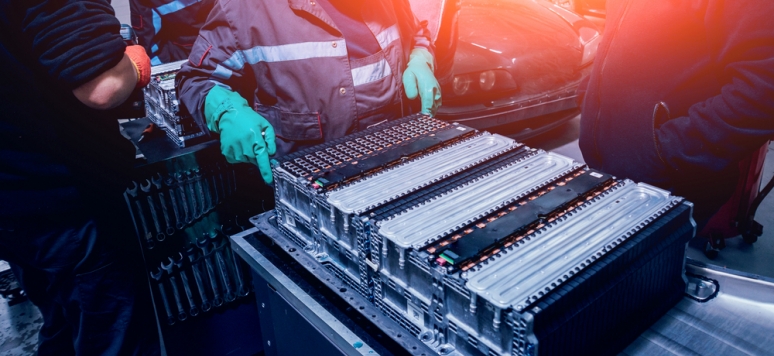
According to the International Energy Agency (IEA), the global fleet of electric vehicles (excluding two/three-wheelers) will reach 245 million vehicles in 2030 – more than 30 times the current level. But while the electric mobility revolution is underway, batteries present several challenges. EV batteries only last about 10 years and the main raw materials used in them are becoming increasingly scarce. In addition, the prices of raw metals are rising and volatile: the price of lithium in 2018 was 241% higher than in 2010, before falling in 2019. Thus, the two major consequences of this EV boom are the increase in demand for lithium, cobalt, and nickel (the key raw materials to produce battery cells) and the challenge of managing lithium-ion battery waste. Players like startup Redwood Materials, cofounded in 2017 by former Tesla CTO J.B. Straubel, are positioning themselves to address battery recycling issues. Indeed, in February 2021, Redwood Materials signed an agreement to recycle scrap and defective battery cells for Envision AESC, the Nissan car battery manufacturer in Smyrna, USA.
When an EV battery reaches the end of its first useful life, manufacturers can either dispose of it, reuse it, or recycle the valuable metals. To reuse batteries, several European automotive companies have already begun installing old EV batteries in multiple energy storage systems, ranging from small-scale residential systems to large-and grid-scale solutions. Nissan, for example, is the first carmaker to have received certification for second-life LEAF batteries to be used in stationary energy storage. Car retrofit – i.e. replacing a thermal engine with a recycled LIB or H2 battery to reduce its emissions (see our newsletter #28) – is also gaining ground. In 2019, Audi announced that it had begun testing second-life EV batteries for factory vehicles.
The other recycling solution is to separately recover the materials from the LIB to give them a second life. As resources are limited, LIB recycling seems to be essential for electric vehicles’ success. The economic benefits of battery recycling are very promising. Based on a recycling rate of 80% after 10 years of use, the profit from the battery recycling market could amount from €0.7 Bn to €1.4 Bn in 2030 (Roland Berger study).
Recycling processes generally involve a physical/mechanical separation followed by pyrolysis and/or a hydrometallurgical process.
- The pyrometallurgical process: nickel, cobalt, and copper are recovered through smelting. Despite the large energy inputs, the recovery rate of this process is low, around 30-40%.
- The hydrometallurgical process: the metal component and the recycled metal solutions are dissolved by leaching. The recovery rate of this process is higher and less-energy intensive, thus preferred by market players. For instance, the German startup Duesenfeld has built a recovery method that combines mechanical, thermodynamic, and hydrometallurgical processes. Compared to the pyrometallurgical process, their method saves 4.8 tonnes of CO2 per tonne of recycled batteries.
Both technologies are used by more and more players. Not only the traditional recycling players but also automotive companies and new startups.
Veolia has been recycling car batteries in France since 2013 and decided in September 2020 to join forces with Solvay to create a circular economy consortium to optimize the recycling of LIB for EVs and hybrids. Regarding automotive players, Audi and recycling player Umicore announced a battery recycling partnership in 2019. For this closed-loop pilot project, Umicore will recover cobalt and nickel from Audi’s e-trons (more than 90% of the cobalt and nickel in their batteries can be recycled) and process them into precursor and cathode materials to produce new batteries from recycled elements. Similarly, Singaporean startup Green Li-ion has a patented multi-cathode processor to recycle all types of Li-ion batteries into 99.9% pure cathodes. This is expected to speed up current recycling processes tenfold and increase profits fourfold.
As this recycling potential begins to be exploited by many players, legislators are supporting these trends through regulations and directives. The EU Commission, whose new Battery Directive is due to be transposed into national law by 2024, wants car and battery manufacturers to set up a comprehensive battery collection and recycling system. The stated aim is that about half the weight of lithium-ion batteries (LIB) should be recycled. In Canada, the Ontario government drafted regulations in May 2019, making the battery producer liable for the collection and management of their product to help create a circular economy. In China, the government has implemented a Battery Recycling and Traceability Management Platform in 2018, where all EV batteries are assigned a unique and traceable ID, facilitating the collection, sorting, and recycling of e-waste.
Although the regulation is being implemented, four major challenges remain:
- The inadequacy of the logistics of LIB collection channels. While this issue should gradually be resolved as recycling accelerates, the question of who will take on the role of logisticians (battery manufacturers, automotive brands, or recycling players, etc.) will remain uncertain if recycling remains centralized.
- The high upfront expenditure required to set up a large-scale LIB recycling plant. Economies of scale are likely to be seen within 5-6 years as recycling becomes more widespread and systematic.
- The requirement for a high LIB recycling efficiency rate, regardless of the LIB chemistry being recycled. The recycling rate is already around 80% and is expected to increase in the coming years, as some startups are developing prototypes capable of recycling more than 90% of the LIB.
- The recycling steps vary according to the different types of batteries (lead-acid, nickel-cadmium, zinc-air, alkaline, …). Thus, recycling facilities need to be adapted to several processes. Even among LIB batteries, the most used for EVs, the process differs according to their composition and recovery rate.
To conclude, lithium-ion batteries are likely to remain the major battery type for EVs in the coming decades (due to their high energy intensity relative to their weight, compared to other batteries such as lead-acid, nickel-cadmium, or zinc-air). There is a need to close the loop to meet the demand for their scarce and expensive raw materials.
2 Key Figures
51 battery recycling startups
registered by Traxcn
Market size expected to reach $12.2Bn by 2025
The size of the battery recycling market is expected to reach $12.2 Bn by 2025, compared to a market of $1.5 Bn in 2019.
3 startups to draw inspiration from
This week, we identified three startups that we can draw inspiration from: Li-Cycle, Green Li-ion and Lohum.
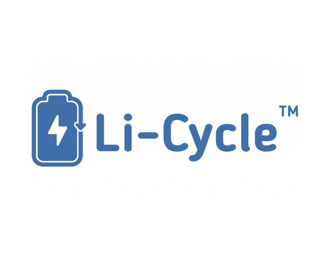
Li-Cycle
Li-Cycle is a Canadian startup that uses a combination of mechanical size reduction and hydro-metallurgical resource recovery techniques to recycle lithium-ion batteries. Their recycling technique does not generate any hazardous product which minimizes transportation liability and lowers costs.
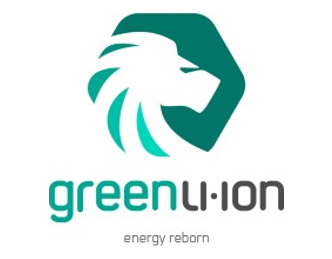
Green Li-ion
It is a Singapore-based start-up which recycles the metals of LIBs (cobalt, nickel, manganese and other expensive metals), recover them, and make them ready to be reused in new batteries. Their patented technology is cleaner, faster, and four times more profitable than current LIB recycling. It is also the only technology to fully rejuvenate the battery cathode
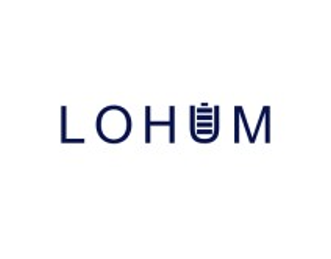
Lohum
Lohum is an Indian start-up manufacturing of Li-ion battery packs and recycling battery components. It provides full lifecycle solutions for manufacturers involved with low-power mobility and storage applications such as electric two-wheelers, rickshaws and inverters. It offers secondary life cycle solutions such as battery recycling to large manufacturers and companies using Li-ion batteries.
123Fab #36
1 topic, 2 key figures, 3 startups to draw inspiration from
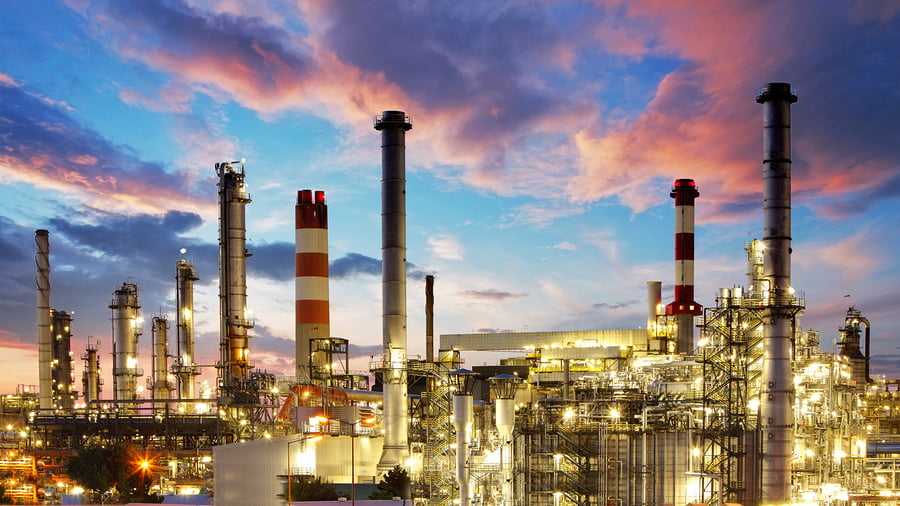
On the one hand, heating and cooling applications are among the largest energy consumers (about half of the total energy consumption). On the other hand, some of the renewable electricity produced is lost due to non-immediate use, and this will continue to accelerate as renewable energy facilities are being developed faster than batteries and storage solutions. The reconciliation of these two issues, converting electrical energy into heat (or cold), is called Power-to-Heat (PtH). Thermal energy is produced by heat pump technologies or electric boilers. In the context of growing environmental awareness, industrials are increasingly looking for technologies that will enable them to shift from fossil-based industrial heating to electrically-based, power-to-heat processes. These industrial heating applications account for almost 20% of global energy consumption.
These renewable power-to-heat technologies help industries to reduce their CO2 emissions and offer higher flexibility in the power system when equipped with smart load management. Industrial application technologies are already mature and commercially available. However, they have yet to be integrated into hybrid heating systems (e.g. with natural gas).
How does it work? The first step is the delivery of electricity from renewable sources to power stations (which may be large centralized heating production stations or decentralized entities). Infrastructures can be equipped with thermal storage systems, such as those of Form Energy, to enable consumers to use the stored heat and thus reduce the demand on the power grid during peak electricity demand periods. Afterwards, there are two technologies to convert electric power into heat: electric boilers and heat pumps. Electric boilers use electricity to heat water, which is then circulated through pipes to provide space heating or stored in hot water tanks for later use. Heat pumps, on the other hand, transfer heat from the surrounding heat sources to buildings and infrastructures. They can fulfill both heating and cooling requirements — typically using between 66% and 80% of the energy contained in the ambient air, water, or ground, and between 20% and 33% electricity to drive the process.
Where is it used? These technologies are applied in different industries, for several uses. The first example is the food & beverage industry, where heat plants are used in Japan for brewing sake and beer. The Suntory production plants, for instance, use a cogeneration system (combined heat and power) that recovers the heat generated from in-house generation and uses it as a heat source for brewing beer and extracting coffee and tea, increasing energy efficiency to 70-80% and reducing CO2 emissions by 20-30%. Another example is the container washing plant in Spain that uses solar thermal heat. 22% of their hot water (80°C) demand is covered by a solar thermal system based on flat plate collectors, and the remainder is covered by a conventional boiler using natural gas. District heating is also a common application of power-to-heat. In Hamburg, Vattenfall operates an electric boiler that uses excess wind generation, thus avoiding wind power curtailment, to generate district heat in Berlin. The units use electricity from renewable energy sources to heat water, which transmit heat to residences and commercial buildings.
More generally, power-to-heat innovations contribute to the transformation of the power sector in 5 ways:
- Reduction of renewable energy curtailment: the excess of energy is used to address heating needs.
- Increased flexibility through load-shifting: heat pumps can offer demand-side flexibility by switching their electricity consumption from high-demand time intervals to low-demand time intervals to convert electric power into stored heat or cold.
- Large-scale energy storage: the surplus heat (resp. cold) produced with renewable energy in summer (resp. winter) can be stored in thermal reservoirs (mainly aquifers), which then can be used to meet the winter (resp. summer) heating demand, thereby reducing the need for non-renewable heat sources during peak times. The most common solution is the use of Phase-Change Materials (PCM), which are efficient against energy loss and leakage and are substances that release or absorb enough energy to maintain a regulated temperature. A great example of such a process is the Canadian project Drake Landing, which uses solar thermal energy and seasonal underground thermal energy storage for a district heating scheme. It supplies a residential community of 52 households that have seen their greenhouse gas emissions cut down by more than 5.5 times per year.
- Grid services provided by aggregators: new “smart” storage heating solutions are designed to take advantage of variations in electricity prices throughout the day and can be remotely controlled by aggregators to both optimize heating costs for consumers and provide grid balancing services to the national grid.
- Increased self-consumption through renewable local generation: consumers with solar rooftop systems can use the locally generated electricity to power heat pumps.
Ultimately, having understood how power-to-heat systems work and what their benefits are, it can be useful to bear in mind the drivers behind their adoption and the regulations that are put in place. Incentives to decarbonize the heating sector are leading to the deployment of heat pumps at a steady pace. On average, the operating costs of using electricity to generate heat are comparable to those of using fossil fuel-based sources. High-performance heat pumps can generate more than 4–5 kWh of useful heat for every 1 kWh of electricity consumed. Furthermore, regulations are being implemented in pioneer countries, like in Germany, where the Renewable Energy Heating Act bans the use of oil burners to heat new buildings and requires all new buildings to use energy generated from renewable energy sources for space and water heating. Similarly, in 2017, Norway’s Ministry of Climate and Environment passed a law banning the use of oils and paraffin from 2020 in heating applications.
To conclude, now that power-to-heat technologies are mature and up-and-running, more incentives should be brought forwards to increase the use of renewable energy in heating and cooling. Domestic and industrial consumers will need to make upfront investments to shift to renewable energy for heating and cooling applications, and schemes that reduce the economic burden on consumers will encourage faster adoption of renewable energy in heating and cooling. However, these schemes need to be tailored to the needs of different consumer segments, types of buildings (residential vs. industrial), and types of heating system (centralized vs. decentralized), as well as to other external factors, such as the climate zone.
2 Key Figures
177 power-to-heat startups
registered by PitchBook, including 100 “thermal energy storage” startups
Market size expected to reach $369M by 2025
The market size of thermal energy storage is expected to reach $369M by 2025, at a CAGR of over 14.4% from 2020.
3 startups to draw inspiration from
This week, we identified three startups that we can draw inspiration from: Malta Inc, Enerstorage, and Heaten
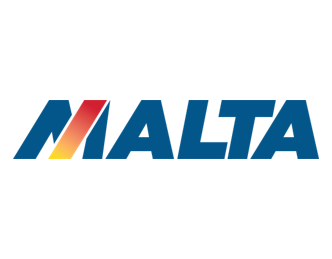
Malta Inc
The US-based startup Malta Inc builds an electro-thermal energy storage system that converts electricity to thermal energy for storage. It later converts the thermal energy back into electrical energy whenever required
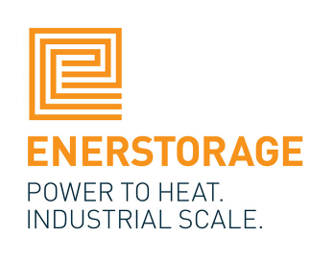
Enerstorage
The German startup Enerstorage sells power-to-heat plants for industries that require a lot of heat. The PtH systems provide an important link between the heat supply and the power grid, regulate the power grids, and thus lead to a successful energy transition.

Heaten
Heaten is an industrial startup that provides heat-to-power and power-to-heat machines. Their very high-temperature heat pumps are based on an innovative piston machine technology, which provides an output temperature up to 165°C, which covers 30% of the energy demand of all industrial heating processes.
123Fab #33
1 topic, 2 key figures, 3 startups to draw inspiration from
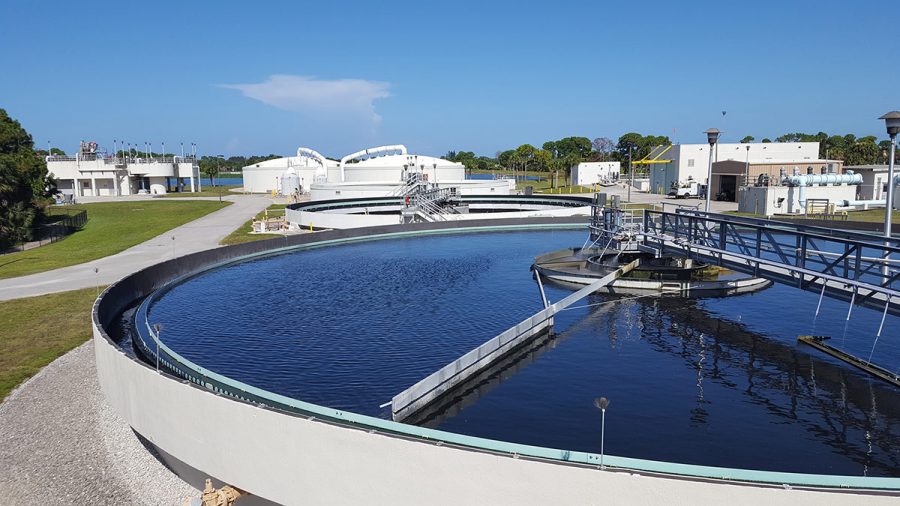
In January 2021, a research team from the Institut National de la Recherche Scientifique (INRS) developed an electrolytic wastewater process that degrades microplastics at the source, instead of a filtration process. Indeed, microplastics can be very present in wastewater, particularly in industrial waster. Industrial wastewater treatment describes the processes for treating wastewater produced by industries as an undesirable by-product.
Given the current pressure on water resources, water contamination issues and the water needs of industries (22% of global use, and 40% in Europe), industrial wastewater treatment is becoming imperative. All the more so as many industries are concerned by contaminated wastewater, be it agriculture (fertilizers), the construction industry (solvents, paints, grease), the food processing industry (organic particulates, animal waste) or oil & gas sectors (grease, oil waste). Treating industrial wastewater has two main benefits, which are reducing industries’ environmental footprint (by reducing waste and harmful contaminants released into the environment) and contributing to the circular economy (by reusing the wastewater to produce energy or fertilizer), thus turning waste into an additional source of revenue. Thereby the market is becoming more competitive and fragmented. However, the industry remains dominated by large companies, relying on their brand and patented product technology. Among the main players are the French companies Suez – which invests €74 million each year in more R&D programs for wastewater treatment solutions — and Veolia, but also international corporations like Ecolab (US) or Thermax Group (India).
The treatment of industrial wastewater requires special methods and technologies that can be divided into three categories:
- Physical treatment methods used to remove solid waste. The main techniques are sedimentation (suspending the insoluble particles from the water and separating them once they have settled to the bottom), aeration, and filtration.
- Chemical treatment methods involve the use of chemicals in the water. Chlorine and ozone are oxidizing chemicals commonly used to kill bacteria and prevent them from reproducing in the water.
- Biological treatment methods use a variety of processes to break down the organic matter present in wastewater. They include aerobic processes (a bacteria decomposes the organic matter and converts it into CO2 that can be used by plants), anaerobic processes (fermentation of the waste at a specific temperature), and composting (wastewater is treated by mixing it with sawdust or other carbon sources).
These three techniques to treat industrial wastewater are used at different stages of the purification process. During the screening phase, physical processes like sedimentation and filtration are used to remove solid waste from the wastewater. For instance, biofiltration is used to ensure that any additional sediment is removed from the wastewater. This is the core of Veolia’s patented technology, Biostyr. The wastewater is then clarified, using physical or biological methods, to remove suspended and floating matters. The refinery industry, for instance, uses a clarifier with a surface skimmer for oil and a bottom rake for solid – also called API separator. When the difference in density is not sufficient to separate oil-wetted solids, air floatation can be used. The company Akvola sells a solution based on a bubble generator and a flotation-filtration process for cleaning hard-to-treat industrial wastewater. The air bubbles attach to contaminants in the waste, decrease their density, and facilitate their separation. Afterward, wastewater is aerated (introduction of air into the water) to allow aerobic biodegradation of the polluting components. Finally, industrial wastewater is disinfected by chemical or biological processes. When it comes to final sewage sludge, it is treated before being sent back to the environment or reused. Sewage sludge is first thickened, then digested and dewatered. During digestion, the sludge produces CO2 and methane, often collected and used to generate power, as is done by AquaGreen. They provide products that focus on converting wastewater sludge into thermal energy, capable of supporting sludge facilities and district heating.
To conclude, innovation and technologies are being developed to treat increasing amounts of industrial wastewater. The environmental footprint (sewage sludge) and energy consumption (2-3% of global energy for water purification) are challenges that need to be addressed in order to reach maturity.
2 Key Figures
98 Industrial wastewater treatment startups
registered by Tracxn
Market size expected to reach $15bn by 2024
The market size of industrial wastewater treatment is expected to reach $15bn by 2025, a CAGR of 5.8% from 2019.
3 startups to draw inspiration from
This week, we identified three startups that we can draw inspiration from: ProSep, Akvola, and EcoWorth Tech.
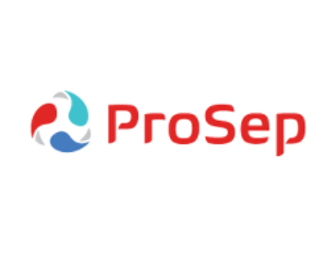
Prosep
Prosep offers several solutions to Oil & Gas businesses. They have a variety of tertiary wastewater treatment technologies, aimed at achieving and maintaining low levels of harmful contaminants in the water streams produced by discharges. Their wastewater treatment solution can be retrofitted into the existing treatment line.
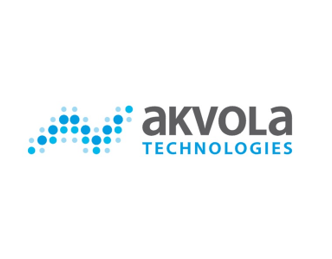
Akvola
Akvola sells environmentally-friendly solutions based on the proprietary MicroGas Fine Bubble Generator and akvoFloat – a flotation-filtration process– to clean hard-to-treat industrial wastewater containing high concentrations of oil (free and emulsified) and suspended solids. It can remove up to 99% of oil & grease and suspended solids
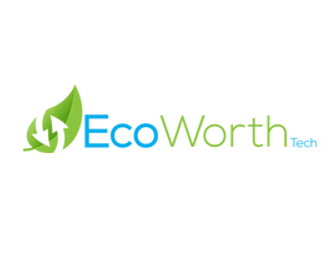
EcoWorth Tech
EcoWorth Tech is a Singaporean startup providing waste-to-worth solutions. They are specialised in transforming waste materials of industrial processes, oil & gas industry and food processing, into reusable products. They notably rely on their “Carbon Fibre Aerogel” technology to treat wastewater.
123Fab #23
1 topic, 2 key figures, 3 startups to draw inspiration from

Over the years, the French government has boosted the financial incentives offered to the biomethane industry to reduce the costs associated with the production and operation of units. Whereas the exemption from the domestic consumption tax on natural gas (TICGN) previously applied to biomethane, the French government has just announced that it will no longer apply from January 2021. France Biométhane, a green gas think-tank, deplores this decision which, according to them, discredits biomethane and favors fossil fuels.
Biomethane, defined as a renewable natural gas with properties close to those of natural gas, may well play a major role in building a sustainable energy future according to the International Energy Agency (IEA). Indeed, there is no need to change the transmission and distribution infrastructures or end-user equipment. Consequently, it can be injected into the natural gas distribution network very easily or used as fuel for vehicles (bio-CNG, bio-LNG). It is also comparable to renewable energy since it emits 10 times less carbon than natural gas, can be stored and offers a solution to the intermittent use of solar and wind energy. Finally, it reduces the pressure on landfills and fits into the circular economy. Therefore, there are reasons to believe that biomethane could become more firmly established in the future. How about its economic viability and technical feasibility?
To date biomethane can be produced in 3 ways:
- The biogas road – which uses wet biowaste. It uses the means of anaerobic digestion to convert the biowaste into biogas. The biogas is then purified to remove the CO2 and other contaminants to produce biomethane.
- The syngas road – which uses dry or semi-dry biowaste. It uses the means of pyro-gasification to convert the biowaste into syngas. The syngas is then cleaned and methanised to convert the hydrogen, carbon monoxide and dioxide into methane.
- The hydrogen road – which uses electricity. It uses the means of electrolysis (or power-to-gas) to convert electricity into hydrogen. The hydrogen is then cleaned and methanised to convert it into methane.
In short, there are three main methods for producing biomethane: anaerobic digestion, pyro-gasification and electrolysis. To date, approximately 90% of the biomethane produced comes from anaerobic digestion and the upgrading of biogas. Among the purifying and upgrading technologies, we can find water scrubbing, adsorption, cryogenic separation, membrane technology, etc.
Waga Energy, a landfill gas-to-energy technology firm, is one of the large players in this segment. In 2018 they notably joined forces with environmental services giant Veolia. Since then, Veolia has been using Waga Energy’s Wagabox® technology to produce biomethane using biogas, which is injected directly into the natural gas grid operated by GRDF. In early October, the two players signed a contract to install a purification unit at the waste storage center in Claye-Souilly. This facility, which should be commissioned by February 2022, will produce biomethane from waste and supply 20,000 households in the Paris region with renewable gas.
Last year, France set an objective of injecting 10% of biomethane (21 TWH) into the country’s gas network by 2030, like Denmark is already doing. Numerous biomethane injection sites have seen the light of the day. To date, 133 biomethane injection sites are producing 2.3 TWH per year. With an average annual growth rate of more than 60% over the last 3-4 years, the French goal seems feasible.
However, production costs remain high when taking into account the cost of input supply, the cost of transformation (into biogas/syngas and then into biomethane), and the cost of injection (connection to the energy grid). The price to produce biomethane reaches €95 compared to €20 for natural gas. This is why the development of biomethane will ultimately depend on the policy framework and if the market conditions remain attractive for the project leaders (green gas feed-in tariffs, stability, or reduction of construction and gas connection costs).
Overall, the optimal uses of biomethane are in the end-sectors where there are fewer low-carbon alternatives (high-temperature heating, petrochemical feedstocks, heavy-duty transport, shipping, etc.). There are also other motivations such as rural development (household digesters), energy security (complementing wind and solar PV or substituting imported natural gas) and urban air quality
Circular economy for industrial waste: Are we getting closer?
For a long time, take-make-waste has been the standard approach to consumption and production. According to a PwC study, 50-75% of the resources used are returned to the natural environment as waste. Thus, manufacturing must give way to more sustainable and circular approaches.
The circular economy is a system of exchange and production which, at all stages of the product life cycle, aims to increase the efficiency of resource use and reduce environmental impact. The circular economy is not limited to industrial waste management, it also includes product design and recycling processes to close the loop. In this newsletter, we will focus on the technologies and methods to limit industrial waste.
In general, industrial waste is collected and then either landfilled (30% of the waste), incinerated, composted (for organic materials), or recycled. Today, a circular economy approach seems more relevant to valorize industrial waste. While the recent takeover of Suez (water and waste management solutions) by Veolia highlights the complexity of the industrial waste market, many other innovative solutions are being developed.
There are several reasons behind the growing interest in the circular economy. The first reason is the global awareness of the climate emergency: 68% of the world’s population considers global warming to be a major threat. The environmental benefits of a circular economy are manyfold: it contributes to the reduction of waste and greenhouse gas emissions, but also to the systematization of recycling. It also reduces dependence on imported resources (raw materials, water, energy), which is critical in the context of resource scarcity. Indeed, COVID-19 has shown the importance of diversifying our value chains and improving Europe’s strategic autonomy by increasing the value of the materials, adopting thoughtful design, reducing recycling costs and ensuring the functioning of the market for secondary raw materials. Another reason lies in technological breakthroughs (digitalization, industry 4.0) which allow new innovative solutions to emerge. In addition to the savings made through the purchase of second-use products, business growth is stimulated and competitiveness is strengthened.
Both private and public players now see industrial waste as an untapped resource to close the loop.
Kalundborg Industrial Symbiosis is a partnership between eleven public and private companies in Denmark. Since 1972, they have developed the world’s first industrial symbiosis, very close to the principles of the circular economy. Its model is based on the fact that a residue from one company becomes a resource for another, which is beneficial for both the environment and the economy. Approximately 135,000 tons per year of fly ash are avoided, and annual gypsum waste is reduced by 80,000 tons. For instance, water from the Statoil refinery is reused to cool the power station; waste heat from the power station is used to heat the district; fly ash from the power station is sent to cement manufacturers and gypsum is sold to a plasterboard manufacturer.
This sustainable initiative, which started nearly 50 years ago, is no longer the only one; many projects are underway, on different scales and led by a wide range of players.
EU-backed projects
The EU supports and funds circular economy innovations for industrial and urban waste management. For instance, the BAMB (Buildings as Material Banks) project aims to reduce construction and demolition waste through a new standardized circular method of building design, allowing the construction sector to recover, repair and reuse building materials. This approach goes beyond the limited and linear life-cycle analysis approaches currently used in the construction industry tools and methodologies.
Large corporation projects
Large corporations are also tackling this issue. ArcelorMittal, one of the biggest recyclers of steel in the world, recycles around 30 million tons every year and ambitions to become a leader in the circular economy. They reuse more than 80% of their steel production residues and by-products, and about 30% or their steel is made from scrap metal instead of iron ore. In Spain for example, ArcelorMittal has found markets for slag (a glass-like by-product that remains after the separation of a given metal), to sell not only what has been produced but also what was been stockpiled in previous years. Other innovative uses of slag include ballasting offshore wind turbines to replace natural materials, thus avoiding the ecosystem disruption that can result from the extraction of these materials from their original habitat.
Startup solutions
It is very interesting to see that smaller players – startups – are also entering this “circular economy waste market”. There are multiple ways to close the loop, startups are positioned in different segments of the value chain:
- In the logistics segment, Cycle Up is the leading professional marketplace for deconstruction materials and building site surplus. Thanks to the marketplace, construction players can sell and exchange their building materials. It also gives advice on the reuse of these materials. This global solution is both a platform and a service provider. All materials can be sold, but especially materials for finishing work (joinery, doors, locks, etc.).
- In the transformation / revalorization segment, Sopraloop recycles and converts post-consumer PET waste (PET bottles, PET trays, etc.) into recycled polyols. They are still working on the prototype, but their solution should enable its users to recycle 7,000 tons of non-recycled complex PET and produce 10,000 tons of recycled polyols per year. In this segment, there is also ZaaK, a startup that focuses on recycling industrial waste into high-value products. Using patented clean technologies, ZaaK intends to revolutionize the building and construction industry with state-of-the-art technologies and high-quality products made from fly ash, a waste by-product from coal-fired power plants.
- In the digital segment, Trinov improves waste management efficiency through data and algorithms. It makes it possible to plot the waste stream generated to simulate the potential use of waste products such as energy recovery, recycling, composting, etc. This modeling allows the financial and environmental impact of each scenario to be measured before making a decision.
- In the waste-to-energy segment, there are mainly solutions for converting organic waste (a subject we’ll dive into in another newsletter). The startup Sistema provides biodigester equipment to produce biogas from organic waste. The biogas can then be used for residential and farming activities.
However, this market faces major financial and legal challenges, slowing down the development of waste services for a circular economy. First, institutional rules and regulations need to be adapted to encourage and promote the development of the circular economy, both nationally and internationally. In the EU, for instance, the common legal basis is still under discussion due to the difference between countries. Secondly, business transformation is costly. Financial incentives are essential to speed up the establishment of the circular economy. Business models also need to be adapted. Even if an asset has been appropriately designed (durable, repairable, etc.) the impact is limited if the business model is not in place to reap the benefits. Finally, multi-stakeholder collaboration is necessary to have a positive impact. To combine environmental and social aspects, collaboration is fundamental to achieve an impact. A good example is Responsible Steel, the industry’s first global multi-stakeholder standard and certification initiative, which aims to develop higher standards, taking into account circularity as well as social and environmental aspects.
Overall, the circular waste economy is still in progress but its future outlook seems promising. Opportunities for industrial waste valorization are arising, thus the sooner it is addressed, the better (both for the planet and for company financials). A major challenge remains to find technical solutions to recycle (particularly difficult for composite materials) and integrate critical materials into a circular economy process.
2 Key Figures
207 Waste Management startups
in the world registered by Crunchbase
Market size expected to reach $435bn by 2023
The global waste management market size was valued at $285bn in 2016 and is expected to reach $435bn by 2023.
3 startups to draw inspiration from
This week, we identified three startups that we can draw inspiration from: Waga Energy, Enosis and Electrochaea.
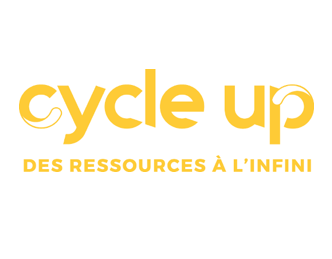
Cycle Up
Cycle up is a marketplace based on the reuse of building materials. The marketplace allows construction actors to buy materials that have already been used or not. It is intended for players in the sector: owners, project owners, architects, demolition workers, builders, it provides access to materials and their reuse solutions.
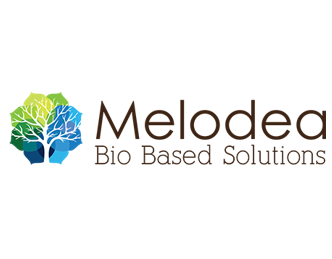
Melodea
Melodea has developed technology for the extraction and industrial production of cellulose nanocrystals (CNCs) from wood pulp and paper production side streams. It extracts CNCs and using them to produce products like water-based adhesives, paints and coatings, or eco-friendly foams.
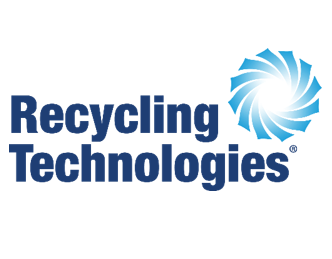
Recycling Technologies
Their modular technology can be mass-produced to recycle plastic waste into feedstock for new plastic production. This solution can be installed at existing waste sites anywhere on the globe to help divert plastic waste away from landfill, incineration and leaking into our environment.