123Fab #52
1 topic, 2 key figures, 3 startups to draw inspiration from
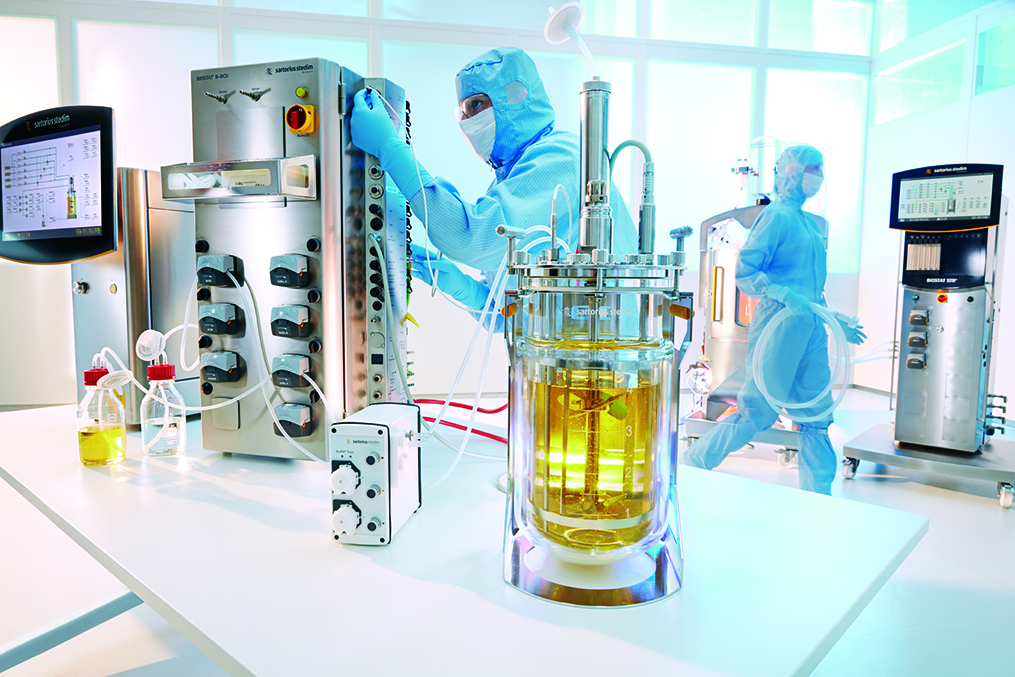
In June 2021, to meet the increased demand for bioprocessing assemblies, Entegris announced that it would invest $30 million to expand three manufacturing facilities. If the idea of using living components in industrial processes is not new – humans were already using yeast to make bread and beer in 4,000 BC – today, bioprocessing is taking it to the next level.
Bioprocessing is any process that uses complete living cells or their components (e.g., bacteria, enzymes, chloroplasts) to obtain their desired products. It is key to several emerging industries and technologies, including the production of renewable biofuels such as ethanol and biodiesel, therapeutic stem cells, or new vaccines. Bioprocessing has several advantages. First, it is an extremely efficient process (a small amount of enzyme quickly yields a lot of product) that operates under mild conditions, thus saving energy. The products are biodegradable and pure and the process is safe (any contamination by an enzyme or known microbe is harmless) and waste-free.
The bioprocess consists of an upstream and a downstream stage. Upstream bioprocessing is the first step in which the microorganisms or cells are grown. They go through several stages of cultivation in a controlled environment within a bioreactor, to be multiplicated. Then, downstream bioprocessing is there to meet purity and quality requirements through cell isolation and purification. Five main types of technologies can be used:
- Conventional bioreactors: These are manufactured systems that support a biologically active environment.
- Single-use bioreactors: These are bioreactors equipped with a disposable bag or instead of a reusable culture vessel. This reduces the cross-contamination risk, requires fewer maintenance requirements and less stringent validation protocols for regulatory approvals.
- Cell culture media: These encompass gels or liquids compounds and nutrients created to support the growth of cells in artificial environments.
- Filtration & concentration: The two types of filtration used in bioprocessing are Direct Flow Filtration (DFF) that uses a single pass of the process fluid through the filter membrane, and Tangential Flow Filtration (TFF), where the process fluid flows parallel (tangential) to the membrane surface.
- Process chromatography: It consists of a pilot- or process-scale system used to separate and purify biomolecules.
The innovations associated with these technologies partly explain the increasing adoption of bioprocessing. First, productivity has increased during the upstream process thanks to new micro-bioreactors (like the Ambr of Sartorius) that allow rapid screening of a large number of media, feeds, and operating conditions such as temperature to determine those producing the highest titers. There are also innovations in the downstream process, with the use of new proteins for purification or improved architecture of the chromatographic resins for faster flow rates. Companies like Pall are continuously working on such innovative solutions. Finally, the switch from batch to continuous bioprocessing, to develop more efficient processes and to reduce time and costs, is enabled by new precisely controlled valves, sensors, and filtration technologies (inline ultrafiltration, diafiltration).
These innovations have an impact on several industries. The main application sectors are biopharmaceuticals, agriculture and food, energy, and waste treatment. Many startups are addressing this surging market in various fields. The American start-up Mango Materials has developed a patented, low-impact biological process that produces bioplastic from methane. Methane from landfill facilities is converted into biodegradable plastic by non-genetically modified bacteria. Their solution is competitive with conventional petrochemical-based plastics and has a capacity of over 10 million pounds of bioplastic per year. Bioprocess engineering in the agriculture and food industry offers opportunities to design and produce new or improved agricultural and food products and their manufacturing processes. In the energy sector, bioprocessing is more and more used for producing biofuels. Start-up TerViva, backed by agricultural-technology businesses, uses the Pongamia plant to produce oil from its seeds. Pongamia produces ten times more amount of oil per acre than soybean and requires only a fraction of resources (water, fertilizers, and pesticides). On top of biodiesel and renewable diesel, Pongamia seed oil can be converted into lubricants, animal feed supplements, or fertilizer. Algae is another way of bio-producing biofuels. The American startup Algenol produces ethanol by using algae, sunlight, CO2, and seawater. When it comes to large corporations, the use of bioprocessing is often limited to specific activities, notably biopharmaceuticals, and the scale. For instance, GE Healthcare (General Electric) reported revenues of $1.5 billion in 2015 from bioprocessing and acquired in 2017 the bioprocessing startup Puridify.
While bioprocessing is a mature field, challenges remain. First of all, the transition from batch to continuous operation is a source of complexity (investment in equipment, process updates, contamination risks, etc.). Furthermore, bioprocessing 4.0 still has progress to make, in terms of digitalization of processes and more systematic data collection and analysis.
To conclude, bioprocessing is becoming an increasingly used technique in various fields. While regulations and norms may be a hindrance in the pharmaceutical industry, in other sectors such as waste treatment, bioprocessing has a huge untapped potential. Single-use bioreactors are expected to be the most widely adopted in the coming years as they are more flexible and can be set up into operation very quickly.
2 Key Figures
180 bioprocessing startups
registered by Tracxn
Global bioprocessing market expected to reach $51.9 Bn by 2028
The global bioprocessing market is estimated at $19.4 Bn in 2021 and is expected to reach $51.9 Bn by 2028, at a CAGR of 16.0%.
3 startups to draw inspiration from
This week, we identified three startups that we can draw inspiration from: Ingenza, Microvi, and Cytoo.
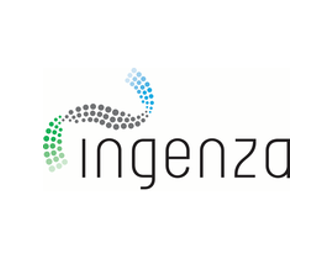
Ingenza
Founded in 2002, Ingenza is an industrial biotechnology startup with a broad customer base across the chemicals, pharmaceuticals, food, feed and fuel industries. They apply synthetic biology to the manufacture of industrial products including enhanced biofuels, sustainable manufacturing of chemicals and the production of protein therapeutics. They also license their proprietary bioprocess technologies.
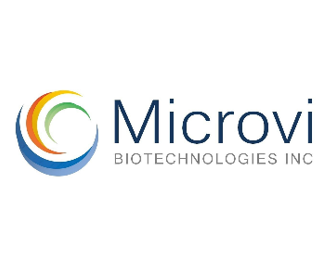
Microvi
Microvi is a biotechnology startup that discovers, develops, manufactures, and commercializes innovative biocatalytic solutions for the water, energy, and chemical industries. Its MicroNiche Engineering platform is a microenvironment of biological systems is precisely designed to enhance microbial life and optimize metabolic performance.
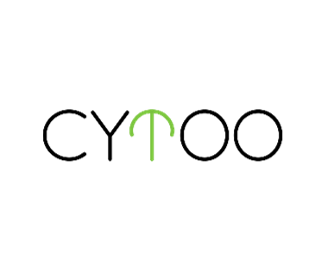
Cytoo
Cytoo is a French startup that develops, manufactures, and distributes products that make cellular analysis robust and reliable by dramatically decreasing cell variability. Their portfolio includes a proprietary cell adhesive micropattern technologies to target High Content Screening and Analysis companies within the large cell biology market.